Como as peças de alta precisão são usinadas
2023-09-22
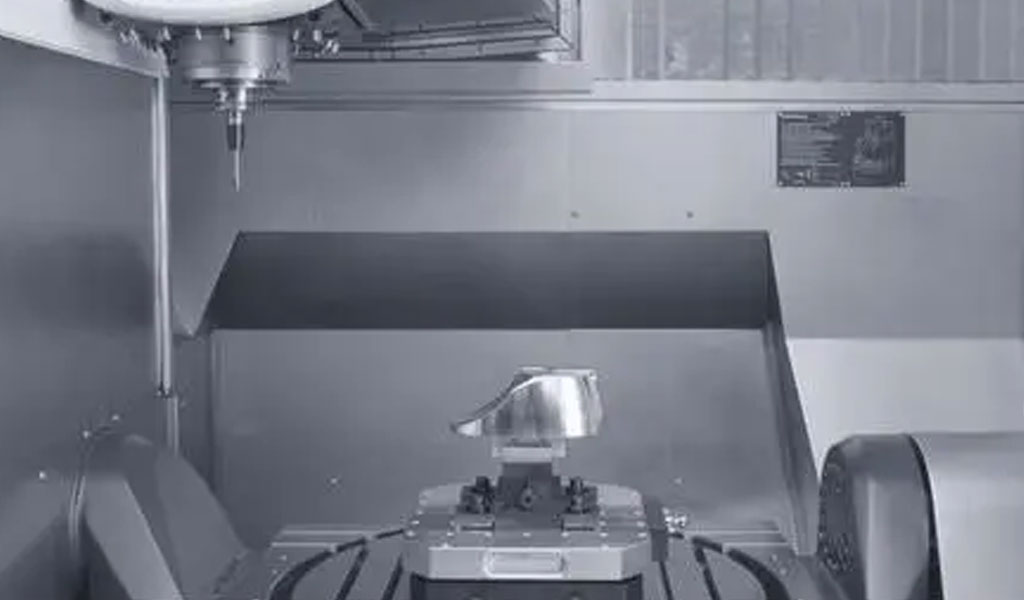
Compreendendo a usinagem de precisão
A usinagem de precisão é a base da fabricação moderna, responsável pela produção de componentes complexos e precisos usados em uma ampla gama de indústrias. Para compreender plenamente o seu significado, vamos explorar os conceitos fundamentais da maquinação de precisão, o seu papel vital em vários setores e a jornada histórica que levou ao seu atual estado de excelência.A. O que é usinagem de precisão?
Usinagem de precisão refere-se a um conjunto de processos de fabricação que removem material de uma peça com alto grau de precisão e controle, resultando em componentes finamente trabalhados com tolerâncias restritas. Este processo transforma matérias-primas, como metais, plásticos ou cerâmicas, em peças precisas que atendem a especificações rigorosas. As principais características da usinagem de precisão incluem:- Precisão: A usinagem de precisão garante que o produto final esteja exatamente em conformidade com o projeto pretendido, com desvio mínimo.
- Tolerâncias apertadas: permite a produção de peças com tolerâncias extremamente restritas, o que significa que os componentes acabados seguem rigorosamente as medidas especificadas.
- Acabamento Superficial Superior: A usinagem de precisão proporciona acabamentos superficiais excepcionais, muitas vezes eliminando a necessidade de processos de acabamento adicionais.
- Geometrias Complexas: pode criar formas, contornos e recursos complexos, tornando-o indispensável na fabricação de componentes com designs complexos.
- Repetibilidade: Precisão Processo de usinagemOs modelos são altamente repetíveis, garantindo qualidade consistente em diversas peças.
- Versatilidade: Pode ser aplicado a uma ampla gama de materiais, tornando-o adequado para diversas indústrias.
B. Importância da Usinagem de Precisão
A usinagem de precisão tem imensa importância em diversas indústrias críticas, impactando vários aspectos de nossas vidas diárias. Aqui estão algumas razões convincentes para sua importância:- Indústria aeroespacial: No setor aeroespacial, a usinagem de precisão é indispensável para a fabricação de componentes que resistem a condições extremas. Motores de aeronaves, pouso engrenagem, e os elementos estruturais dependem de peças usinadas com precisão para segurança e desempenho.
- Dispositivos Médicos: Dispositivos médicos como instrumentos cirúrgicos, próteses e dispositivos implantáveis exigem usinagem de precisão para biocompatibilidade, exatidão e segurança do paciente.
- Setor automotivo: Peças usinadas com precisão são essenciais para a indústria automotiva garantir a confiabilidade e a eficiência dos veículos. Componentes como peças de motor, sistemas de transmissão e mecanismos de freio dependem de usinagem precisa.
- Eletrônica e semicondutores: A usinagem de precisão é fundamental na produção de componentes microeletrônicos e dispositivos semicondutores, onde tolerâncias minúsculas são essenciais para a funcionalidade.
- Setor de energia: A indústria de energia depende da usinagem de precisão para a produção de peças críticas utilizadas na geração de energia, incluindo turbinas, geradores e componentes de transmissão.
- Fabricação de ferramentas e matrizes: A usinagem de precisão é crucial na fabricação de ferramentas e matrizes, que, por sua vez, são utilizadas para criar inúmeros outros produtos.
- Eletrónica de Consumo: A produção de smartphones, laptops e outros produtos eletrônicos de consumo se beneficia da usinagem de precisão para garantir designs elegantes e funcionalidade ideal.
- Pesquisa e Desenvolvimento: Pesquisadores e cientistas dependem de componentes usinados com precisão para experimentos, protótipos e equipamentos de laboratório.
C. Perspectiva Histórica
A jornada da usinagem de precisão remonta a civilizações antigas, onde artesãos qualificados usavam ferramentas rudimentares para moldar materiais. No entanto, a precisão alcançada naquela época era limitada em comparação com os padrões contemporâneos.- Usinagem de Precisão Antecipada: A revolução industrial dos séculos 18 e 19 marcou um período crucial no desenvolvimento da usinagem de precisão. A invenção de máquinas-ferramentas, como tornos e fresadoras, revolucionou a fabricação ao permitir maior precisão e consistência.
- II Guerra Mundial: A usinagem de precisão desempenhou um papel fundamental na Segunda Guerra Mundial, pois foi essencial para a produção de equipamentos militares com a precisão e uniformidade exigidas. Esta era testemunhou avanços nas técnicas de usinagem e o surgimento de novos materiais.
- Avanços pós-guerra: O período pós-guerra viu um aumento nas inovações tecnológicas, incluindo o uso de máquinas de controle numérico computadorizado (CNC). usinagem CNC permitiu operações automatizadas e altamente precisas, inaugurando uma nova era de fabricação.
- A era digital: A integração de computadores e software nos processos de usinagem elevou ainda mais a precisão da usinagem. As máquinas CNC modernas podem executar operações complexas com precisão incomparável, tornando-as indispensáveis no cenário de fabricação atual.
Materiais e seu significado
Os materiais são a base da usinagem de precisão, e a seleção do material certo desempenha um papel fundamental na produção de peças de alta precisão. Nesta seção, nos aprofundaremos na importância de selecionar os materiais apropriados, compreender a importância das propriedades dos materiais e explorar os vários fatores que afetam a usinabilidade.A. Seleção de Materiais
A escolha dos materiais na usinagem de precisão é uma decisão crítica que impacta diretamente no desempenho, durabilidade e funcionalidade do produto final. Os fabricantes devem considerar vários fatores ao selecionar os materiais:- Adequação do Material: O material deve ser adequado à aplicação pretendida. Diferentes indústrias e aplicações têm requisitos variados, como resistência à temperatura, resistência à corrosão e condutividade elétrica.
- Propriedades mecânicas: Propriedades mecânicas como resistência à tração, dureza e ductilidade são cruciais. Por exemplo, na indústria aeroespacial, materiais com alta resistência à tração são preferidos para componentes estruturais.
- Propriedades térmicas: Algumas aplicações requerem materiais com excelente condutividade térmica ou resistência a altas temperaturas. Isto é especialmente importante em indústrias como geração de energia e eletrônica.
- Resistência à Corrosão: Em ambientes onde a corrosão é uma preocupação, são preferidos materiais com alta resistência à corrosão, como aço inoxidável ou titânio.
- Considerações sobre peso: Indústrias como a automotiva e a aeroespacial geralmente priorizam materiais leves, como alumínio ou compostos de fibra de carbono, para reduzir o consumo de combustível e melhorar o desempenho.
- Restrições de custo: O custo é um fator significativo na seleção do material. Os materiais de alto desempenho podem ser caros, por isso os fabricantes devem encontrar um equilíbrio entre desempenho e relação custo-benefício.
- Conformidade Regulamentar: Em setores como o de saúde, os materiais devem atender a padrões regulatórios rigorosos de biocompatibilidade e segurança.
- Disponibilidade: A disponibilidade de materiais e suas fontes também afetam a seleção. Algumas ligas ou compósitos especializados podem ter disponibilidade limitada.
B. Propriedades dos materiais
Compreender as propriedades dos materiais é crucial para a usinagem de precisão. Aqui estão algumas propriedades importantes dos materiais e seu significado:- Resistência à Tração: A resistência à tração mede a capacidade de um material de suportar uma força de tração sem quebrar. É essencial para componentes estruturais e peças sujeitas a esforços mecânicos.
- Dureza: A dureza indica a resistência de um material à deformação e ao desgaste. Materiais duros são adequados para ferramentas de corte, enquanto materiais mais macios podem ser preferidos para determinadas aplicações, como vedações.
- Ductilidade: Ductilidade refere-se à capacidade de um material de se deformar sem quebrar quando submetido a tensão de tração. Os materiais dúcteis são mais fáceis de moldar, mas podem não ser adequados para aplicações que exigem rigidez.
- Condutividade Térmica: Materiais com alta condutividade térmica dissipam o calor com eficiência. Esta propriedade é vital em aplicações onde o controle de temperatura é crítico.
- Condutividade elétrica: A condutividade elétrica é essencial em componentes eletrônicos e elétricos, onde os materiais devem facilitar o fluxo de eletricidade.
- Propriedades magnéticas: As propriedades magnéticas são significativas em indústrias como eletromagnética e eletrônica, onde os materiais podem precisar ser ferromagnéticos ou não magnéticos.
- Resistência química: Os materiais devem resistir à corrosão química em ambientes onde estão expostos a ácidos, bases ou outras substâncias corrosivas.
C. Fatores de usinabilidade
Usinabilidade refere-se à facilidade com que um material pode ser usinado, cortado ou moldado. É influenciado por vários fatores, incluindo:- Dureza Material: Materiais mais macios são geralmente mais fáceis de usinar, enquanto materiais mais duros podem exigir ferramentas e técnicas especializadas.
- Formação de cavacos: A formação e evacuação de cavacos durante a usinagem afetam a eficiência do processo e o acabamento superficial.
- Desgaste da ferramenta: Diferentes materiais podem causar vários graus de desgaste da ferramenta, afetando a velocidade e o custo da usinagem.
- Refrigerante e Lubrificação: A refrigeração e a lubrificação adequadas são essenciais para reduzir o atrito, o calor e o desgaste da ferramenta durante a usinagem.
- velocidade de corte: A velocidade com que a ferramenta de corte se move através do material afeta tanto a produtividade quanto a qualidade da superfície usinada.
- Material de ferramenta: A escolha do material da ferramenta de corte, como metal duro ou aço rápido, depende do material que está sendo usinado.
- Parâmetros de corte: O ajuste dos parâmetros de corte, como avanço e profundidade de corte, pode otimizar o processo de usinagem para materiais específicos.
Máquinas-ferramentas para usinagem de precisão
As máquinas-ferramenta são o coração da usinagem de precisão, possibilitando a transformação de matérias-primas em peças de alta precisão. Nesta seção, exploraremos quatro tipos principais de máquinas-ferramentas usadas na usinagem de precisão: centros de usinagem CNC, tornos, retificadoras e EDM (usinagem por descarga elétrica). Cada uma dessas máquinas desempenha um papel único na produção de componentes precisos.A. Centros de usinagem CNC
Os centros de usinagem CNC (Controle Numérico Computadorizado) são versáteis e amplamente utilizados em usinagem de precisão. São sistemas automatizados que controlam o movimento de ferramentas de corte e peças com precisão excepcional. Aqui está uma visão geral dos centros de usinagem CNC e seu significado:- Versatilidade: Os centros de usinagem CNC podem realizar várias operações de usinagem, incluindo fresamento, perfuração e rosqueamento. Essa versatilidade permite a produção de peças complexas com múltiplas funcionalidades.
- Alta precisão: O controle computadorizado das máquinas CNC garante o posicionamento preciso da ferramenta e resultados consistentes, tornando-as ideais para peças com tolerâncias restritas.
- Automação: Os centros de usinagem CNC podem operar continuamente, com intervenção humana mínima. Essa automação aumenta a eficiência e reduz o risco de erros.
- Geometrias Complexas: Eles se destacam na usinagem de formas e contornos complexos, tornando-os adequados para indústrias como a aeroespacial, onde componentes complexos são comuns.
- Resultados repetíveis: As máquinas CNC oferecem excelente repetibilidade, garantindo que cada peça produzida corresponda às especificações exatas do projeto.
- Tempos de configuração reduzidos: Os centros de usinagem CNC podem ser programados para alternar rapidamente entre diferentes tarefas, minimizando os tempos de configuração e aumentando a eficiência da produção.
B. Tornos
Os tornos são usados para criar peças cilíndricas girando uma peça enquanto uma ferramenta de corte remove o material de sua superfície externa. São essenciais para a produção eixos, pinos e outros componentes com simetria rotacional. Os pontos principais sobre tornos incluem:- Peças cilíndricas: Os tornos são especializados na produção de componentes cilíndricos ou tubulares, incluindo aqueles com roscas ou ranhuras intrincadas.
- Altas velocidades: Operam em altas velocidades, tornando-os adequados para peças que requerem acabamento liso e preciso.
- Operação de eixo único: A maioria dos tornos são de eixo único, com foco na modelagem da superfície externa da peça.
- Eficiente para produção em massa: O torneamento é altamente eficiente para a produção de peças em massa com desperdício mínimo de material.
- Máquinas de torno: Tornos manuais e controlados por CNC são tornos comumente usados, oferecendo uma variedade de recursos.
C. Máquinas retificadoras
As retificadoras são projetadas para acabamento superficial de precisão e modelagem de materiais duros ou abrasivos. Eles são cruciais para alcançar tolerâncias extremamente restritas e acabamentos superficiais superiores. Veja por que as retificadoras são importantes:- Precisão em nível de mícron: As retificadoras podem atingir precisão de nível mícron, o que as torna essenciais para aplicações que exigem o mais alto nível de precisão.
- Remoção de Material: Removem material por abrasão, permitindo a correção de imperfeições superficiais e alcançando lisura excepcional.
- Retificação de ferramentas e cortadores: Além da retificação superficial, existem retificadoras especializadas para afiar ferramentas de corte e produzir perfis precisos.
- Variedade de métodos de moagem: Diferentes tipos de retificadoras, incluindo retificadoras de superfície, retificadoras cilíndricas e retificadoras centerless, atendem a diversas necessidades de usinagem.
- Materiais Endurecidos: A retificação é particularmente adequada para materiais endurecidos, como aço para ferramentas e cerâmica, onde os métodos de usinagem tradicionais podem ser ineficazes.
D. EDM (usinagem por descarga elétrica)
EDM, ou Usinagem por Descarga Elétrica, é um processo de usinagem não tradicional que utiliza descargas elétricas para moldar materiais. É ideal para criar peças complexas e delicadas onde as ferramentas de corte tradicionais podem causar danos. Os principais aspectos do EDM incluem:- Sem contato físico: A EDM não envolve contato físico direto entre a ferramenta e a peça, minimizando o risco de desgaste da ferramenta e danos a materiais frágeis.
- Alta precisão: Pode atingir alta precisão e qualidade de acabamento superficial, mesmo com materiais excepcionalmente duros.
- EDM de fio e EDM chumbada: Existem dois tipos principais de máquinas EDM: corte de fio EDM, que usa um eletrodo de arame, e EDM chumbada, que usa um eletrodo moldado.
- Formas Complexas: A EDM pode produzir formas complexas, como matrizes e moldes, com detalhes intrincados e características finas.
- Zona afetada pelo calor: Como o EDM não gera calor na peça de trabalho, é adequado para materiais sensíveis ao calor, como ligas aeroespaciais.
- Processo Lento: A EDM é relativamente lenta em comparação com outros métodos de usinagem, tornando-a mais adequada para trabalhos de baixa quantidade e alta precisão.
Ferramentas de corte e ferramentas
As ferramentas de corte estão na vanguarda da usinagem de precisão, servindo como instrumentos que moldam e transformam matérias-primas em peças de alta precisão. Nesta seção, exploraremos os vários tipos de ferramentas de corte, a importância dos revestimentos das ferramentas e os fatores que afetam a vida útil e o desgaste da ferramenta.A. Tipos de ferramentas de corte
A usinagem de precisão depende de uma ampla gama de ferramentas de corte, cada uma projetada para tarefas e materiais específicos. A escolha da ferramenta de corte influencia muito a eficiência e a precisão do processo de usinagem. Aqui estão alguns tipos comuns de ferramentas de corte:- Fresas de topo: As fresas de topo são ferramentas versáteis usadas para operações de fresamento. Eles têm múltiplas arestas de corte e podem remover material da peça de trabalho de várias maneiras, incluindo faceamento, contorno e ranhuras.
- Brocas: As brocas são projetadas para criar furos em peças de trabalho. Eles vêm em vários formatos, incluindo brocas helicoidais, brocas centrais e brocas intercambiáveis.
- Pastilhas para torneamento: São usados em tornos para moldar peças cilíndricas. As pastilhas para torneamento estão disponíveis em uma variedade de formatos e materiais para atender a diferentes aplicações.
- Fresas: As fresas vêm em diferentes formatos, como fresas de facear, fresas de bolas e fresas de ranhura, e são usadas em fresadoras para criar vários recursos na peça de trabalho.
- Escareadores: Os alargadores são usados para acabamento e dimensionamento de furos previamente perfurados em dimensões precisas. Eles garantem superfícies de furo suaves e precisas.
- Torneiras e matrizes: Estas ferramentas de corte são usadas para operações de rosqueamento. As torneiras criam threads internos, enquanto as matrizes criam threads externos.
- mós: Os rebolos são ferramentas abrasivas usadas para retificação de superfícies de precisão. Eles estão disponíveis em vários materiais abrasivos e tamanhos de grão.
- Broches: Broches são ferramentas especializadas usadas para cortar formas e perfis internos e externos, como rasgos de chaveta e ranhuras.
- Rebaixamentos e Escareadores: Estas ferramentas são usadas para criar reentrâncias ou chanfros em torno de furos para prendedors.
- Barras chatas: As barras de mandrilar são usadas em operações de mandrilamento para ampliar furos existentes com precisão.
B. Revestimentos de ferramentas
Os revestimentos de ferramentas são finas camadas de material aplicadas às ferramentas de corte para melhorar seu desempenho e durabilidade. Esses revestimentos oferecem diversas vantagens:- Fricção reduzida: Revestimentos como nitreto de titânio (TiN) e carbonitreto de titânio (TiCN) reduzem o atrito entre a ferramenta e a peça, proporcionando um corte mais suave e maior vida útil da ferramenta.
- Dureza aprimorada: Os revestimentos aumentam a dureza da superfície da ferramenta, tornando-a mais resistente ao desgaste e prolongando a vida útil da ferramenta.
- Resistência ao calor melhorada: Os revestimentos podem suportar altas temperaturas geradas durante a usinagem, reduzindo o desgaste da ferramenta relacionado ao calor e aumentando as velocidades de corte.
- Propriedades anti-acúmulo: Alguns revestimentos possuem propriedades antiadesivas, evitando o acúmulo de material nas arestas de corte da ferramenta.
- Lubricidade aumentada: As ferramentas revestidas melhoraram a lubricidade, reduzindo a necessidade de refrigeração excessiva e melhorando o escoamento de cavacos.
C. Vida útil e desgaste da ferramenta
Compreender a vida útil e o desgaste da ferramenta é crucial para otimizar os processos de usinagem e minimizar os custos de produção. A vida útil da ferramenta refere-se ao tempo que uma ferramenta de corte permanece eficaz antes de ser necessária substituição ou recondicionamento. Vários fatores influenciam a vida útil e o desgaste da ferramenta:- velocidade de corte: Velocidades de corte mais altas podem levar a um maior desgaste da ferramenta devido às temperaturas mais altas geradas durante a usinagem. A seleção adequada das velocidades de corte é essencial para equilibrar a vida útil e a produtividade da ferramenta.
- Taxa de alimentação: A taxa na qual a ferramenta de corte avança na peça afeta o desgaste da ferramenta. Taxas de avanço altas podem acelerar o desgaste, enquanto taxas de avanço mais baixas podem prolongar a vida útil da ferramenta.
- Profundidade do corte: A profundidade do corte influencia a quantidade de material removido por passe. Cortes mais profundos podem aumentar o desgaste da ferramenta, portanto, otimizar a profundidade é fundamental.
- Dureza Material: O corte de materiais duros pode acelerar o desgaste da ferramenta. Ferramentas e revestimentos especializados são usados para usinar materiais duros de maneira eficaz.
- Refrigerante e Lubrificação: O líquido refrigerante e a lubrificação adequados ajudam a dissipar o calor e reduzir o atrito, prolongando a vida útil da ferramenta.
- Material de ferramenta: O material do qual a ferramenta de corte é feita afeta sua resistência ao desgaste. Materiais como metal duro e cerâmica oferecem excelente resistência ao desgaste.
- Geometria da ferramenta: A geometria da ferramenta de corte, incluindo ângulo de saída, ângulo de relevo e projeto do quebra-cavacos, desempenha um papel significativo nos padrões de desgaste.
- Material da peça de trabalho: O tipo de material que está sendo usinado afeta o desgaste da ferramenta. Materiais abrasivos podem levar a um desgaste mais rápido da ferramenta.
Processos de Usinagem de Precisão
Os processos de usinagem de precisão são os métodos pelos quais as matérias-primas são transformadas em peças de alta precisão com tolerâncias restritas e acabamentos superficiais excepcionais. Nesta seção, exploraremos cinco processos principais de usinagem de precisão: Torneamento, Fresamento, Furação, Retificação e Usinagem por Descarga Elétrica (EDM). Cada um desses processos serve a um propósito único e é empregado com base nos requisitos específicos da peça.A. Virando
O torneamento é um processo de usinagem usado principalmente para moldar peças cilíndricas. Envolve girar uma peça de trabalho enquanto uma ferramenta de corte de ponta única remove o material da superfície externa. Aqui estão os principais aspectos do torneamento:- Peças cilíndricas: O torneamento é ideal para a produção de componentes cilíndricos, como eixos, pinos e luvas.
- Simetria rotacional: É adequado para peças que requerem simetria rotacional, pois a peça gira em um torno enquanto a ferramenta de corte a molda.
- Várias Operações: O torneamento pode realizar várias operações, incluindo faceamento, torneamento (redução do diâmetro), torneamento cônico e rosqueamento.
- Corte de ponto único: Uma única ferramenta de corte remove material em um movimento contínuo, resultando em remoção eficiente de material.
- Máquinas de torno: Tornos manuais e controlados por CNC são comumente usados para operações de torneamento.
B. Fresagem
O fresamento é um processo versátil de usinagem de precisão que emprega ferramentas de corte multiponto para remover material de uma peça. É adequado para criar uma ampla variedade de formas e recursos. Os principais aspectos da fresagem incluem:- Versatilidade: O fresamento pode produzir superfícies planas, ranhuras, bolsões e contornos complexos. É usado para usinagem 2D e 3D.
- Corte multiponto: Múltiplas arestas de corte na ferramenta interagem com a peça simultaneamente, permitindo uma remoção eficiente de material.
- Tipos de Fresagem: O fresamento pode ser realizado usando vários tipos de fresas, incluindo fresas de topo, fresas de face e moinhos de bolas.
- Centros de usinagem CNC: As fresadoras controladas por CNC oferecem controle preciso sobre o movimento da ferramenta e são amplamente utilizadas na usinagem moderna.
- Altas velocidades: A fresagem pode ser realizada em altas velocidades, permitindo uma produção eficiente.
C. Perfuração
A perfuração é um processo de usinagem de precisão usado para criar furos em peças de trabalho. É uma operação fundamental em diversos setores. Os principais aspectos da perfuração incluem:- Criação de furo: As furadeiras usam ferramentas especializadas chamadas brocas para remover material e criar furos de diâmetros específicos.
- Tipos de exercícios: Diferentes tipos de brocas estão disponíveis, incluindo brocas helicoidais, brocas centrais e brocas intercambiáveis, cada uma projetada para aplicações específicas.
- Precisão: O posicionamento e o alinhamento precisos são essenciais na perfuração para garantir que os furos sejam criados com precisão.
- Velocidade e taxa de alimentação: Parâmetros de furação como velocidade de rotação e taxa de avanço são essenciais para atingir as dimensões desejadas do furo.
- Refrigerante e Lubrificação: Líquido refrigerante e lubrificação adequados são usados para dissipar o calor e reduzir o atrito durante a perfuração.
D. Moagem
A retificação é um processo de usinagem de precisão que utiliza discos abrasivos para remover material e obter tolerâncias e acabamentos superficiais extremamente rígidos. Os principais aspectos da moagem incluem:- Precisão excepcional: A retificação pode atingir precisão de nível mícron, tornando-a ideal para aplicações que exigem a mais alta precisão.
- Revestimento de superfície: Produz acabamentos superficiais superiores, muitas vezes eliminando a necessidade de processos de acabamento adicionais.
- Materiais: A retificação é adequada para materiais duros e abrasivos, incluindo aço endurecido, cerâmica e carbonetos.
- Variedade de métodos de moagem: Diferentes tipos de retificadoras, como retificadoras de superfície, retificadoras cilíndricas e retificadoras centerless, atendem a diversas necessidades de usinagem.
- Refrigerante: A refrigeração adequada é essencial na retificação para evitar superaquecimento e manter a integridade do rebolo.
E. Usinagem por Descarga Elétrica (EDM)
EDM, ou Usinagem por Descarga Elétrica, é um processo de usinagem de precisão não tradicional que utiliza descargas elétricas para remover material. É particularmente adequado para usinar formas complexas e intrincadas, bem como materiais duros e resistentes ao calor. Os principais aspectos do EDM incluem:- Usinagem sem contato: EDM não envolve contato direto entre a ferramenta e a peça, reduzindo o risco de desgaste e danos à ferramenta.
- Alta precisão: O EDM pode atingir alta precisão, tornando-o adequado para aplicações onde tolerâncias rígidas são essenciais.
- Formas Complexas: É excelente na usinagem de formas complexas, matrizes, moldes e componentes com detalhes finos.
- EDM de fio e EDM chumbada: Existem dois tipos principais de máquinas de EDM: EDM de fio, que usa um eletrodo de fio, e EDM de chumbada, que usa um eletrodo moldado.
- Processo Lento: A EDM é relativamente lenta em comparação com outros métodos de usinagem, tornando-a mais adequada para trabalhos de baixa quantidade e alta precisão.
Tolerâncias e Controle de Qualidade
A usinagem de precisão exige atenção meticulosa aos detalhes e um compromisso rigoroso com o controle de qualidade para garantir que as peças atendam aos padrões especificados. Nesta seção, exploraremos três aspectos críticos do controle de qualidade em usinagem de precisão: Dimensionamento e Tolerância Geométrica (GD&T), Controle Estatístico de Processo (SPC) e Garantia de Qualidade.A. Dimensionamento e Tolerância Geométrica (GD&T)
Dimensionamento e Tolerância Geométrica, muitas vezes abreviado como GD&T, é um sistema usado para definir e comunicar as variações permitidas em tamanho, forma, orientação e localização de recursos em uma peça. GD&T é vital na usinagem de precisão pelos seguintes motivos:- Comunicação precisa: GD&T fornece uma linguagem padronizada para engenheiros, projetistas e maquinistas comunicarem com precisão a intenção do projeto e os requisitos dimensionais.
- Esclarecimento sobre tolerância: Ajuda a definir a variação aceitável nas dimensões críticas, garantindo que todas as partes interessadas compreendam os desvios permitidos.
- Qualidade aprimorada: GD&T promove melhoria da qualidade reduzindo a ambiguidade nas especificações de projeto, minimizando o risco de erros durante a usinagem.
- Eficiência de custos: Especificações claras de GD&T podem levar à redução dos custos de fabricação, pois é menos provável que as peças sejam descartadas ou exijam retrabalho devido a mal-entendidos ou interpretações incorretas.
- Geometria Complexa: É particularmente útil para peças com geometrias complexas, garantindo que todas as características sejam fabricadas de acordo com as especificações desejadas.
B. Controle Estatístico de Processo (CEP)
O Controle Estatístico de Processo (CEP) é uma metodologia de controle de qualidade que utiliza técnicas estatísticas para monitorar e controlar o processo de usinagem. O SPC é essencial na usinagem de precisão pelos seguintes motivos:- Monitoramento de processo: O SPC auxilia no monitoramento dos processos de usinagem em tempo real, identificando variações ou desvios dos parâmetros desejados.
- Detecção Precoce de Problemas: Ao monitorar continuamente o processo, o SPC permite a detecção precoce de problemas que podem levar a peças fora das especificações, reduzindo desperdícios e retrabalhos.
- Tomada de decisão baseada em dados: O SPC depende de dados e análises estatísticas para tomar decisões informadas sobre ajustes de processo, garantindo que o processo de usinagem permaneça dentro de limites aceitáveis.
- Consistência Melhorada: O SPC promove a consistência do processo e reduz a probabilidade de produção de peças não conformes.
- Redução de sucata e retrabalho: Ao identificar e abordar prontamente as variações do processo, o SPC minimiza a produção de peças defeituosas, reduzindo os custos de refugo e retrabalho.
C. Garantia de qualidade em usinagem de precisão
A garantia de qualidade na usinagem de precisão abrange uma abordagem abrangente para garantir que as peças fabricadas atendam ou excedam os padrões de qualidade especificados. Envolve vários elementos, incluindo:- Documentação do processo: A documentação detalhada dos processos de usinagem, incluindo procedimentos operacionais padrão (SOPs) e instruções de trabalho, garante que cada etapa seja executada de forma consistente.
- Inspeção e Medição: Inspeção e medição rigorosas usando instrumentos de precisão e técnicas de metrologia verificam se as peças estão em conformidade com tolerâncias e padrões de qualidade especificados.
- calibragem: A calibração regular de equipamentos de usinagem e instrumentos de medição é essencial para manter a precisão e a rastreabilidade.
- Verificação de Material: A verificação das propriedades, composição e qualidade do material é fundamental para garantir que o material utilizado atenda aos requisitos do projeto.
- Treinamento de funcionário: Programas de treinamento e desenvolvimento de habilidades para maquinistas e pessoal de controle de qualidade garantem que eles sejam proficientes em suas funções e responsabilidades.
- Análise de causa raiz: Quando peças não conformes são identificadas, a análise da causa raiz é conduzida para determinar a origem do problema e implementar ações corretivas.
- Melhoria Contínua: Uma cultura de melhoria contínua promove a inovação e impulsiona melhorias contínuas nos processos de usinagem e procedimentos de controle de qualidade.
- Feedback dos nossos clientes: Coletar e analisar o feedback do cliente ajuda a identificar áreas de melhoria e alinha os processos de usinagem com as expectativas do cliente.
Conclusão
A. A arte e a ciência da usinagem de precisão
A usinagem de precisão está na interseção entre arte e ciência, onde criatividade, habilidade e inovação convergem para produzir peças de alta precisão que impulsionam as indústrias e moldam o mundo moderno. É ao mesmo tempo uma forma de arte, que exige a habilidade e a experiência de maquinistas que transformam matérias-primas em obras de excelência em engenharia, e uma ciência que depende de tecnologia de ponta, ciência de materiais e processos avançados para alcançar uma precisão incomparável. A jornada da usinagem de precisão nos leva através da compreensão dos materiais e suas propriedades, do domínio das ferramentas e máquinas de corte e do controle meticuloso de processos e tolerâncias. Abrange a linguagem do dimensionamento geométrico e tolerância, a vigilância do controle estatístico do processo e o compromisso com a garantia de qualidade. A usinagem de precisão desempenha um papel fundamental em diversos setores, desde aeroespacial e automotivo até dispositivos médicos e eletrônicos, moldando tudo, desde motores de aeronaves até juntas artificiais e microchips. Ele permite a criação de componentes que operam com precisão e confiabilidade incomparáveis, muitas vezes ultrapassando os limites do que é possível.B. Considerações Finais
Ao concluirmos esta exploração da usinagem de precisão, fica claro que este campo não trata apenas da criação de peças; trata-se da criação de possibilidades. A busca pela precisão impulsiona a inovação, ultrapassando os limites do que pode ser alcançado. Quer se trate do delicado trabalho artesanal necessário para criar as intrincadas engrenagens de um relógio ou da tecnologia avançada necessária para fabricar componentes aeroespaciais complexos, a usinagem de precisão está no centro de tudo. O futuro da usinagem de precisão é promissor. Os avanços na ciência dos materiais, na automação e nas tecnologias digitais continuam a remodelar o cenário. A miniaturização, a impressão 3D e as práticas de produção sustentáveis estão a tornar-se cada vez mais proeminentes, abrindo novos horizontes para a indústria. Num mundo onde a precisão é mais importante do que nunca, a maquinação de precisão continua a ser um pilar indispensável da engenharia moderna. É uma prova da engenhosidade humana e da nossa busca incessante pela excelência em todas as facetas da fabricação. À medida que cresce a procura por maior precisão e componentes mais complexos, a maquinação de precisão continuará a evoluir, enfrentando os desafios de amanhã com a mesma dedicação e precisão que a definiram durante séculos.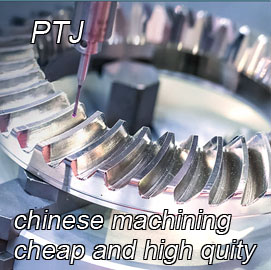
Serviços
- 5 eixos de usinagem
- Fresagem CNC
- Torneamento CNC
- Indústrias de usinagem
- Processo de usinagem
- Tratamento da superfície
- Usinagem de Metal
- Usinagem de Plástico
- Molde de metalurgia do pó
- Fundição
- Galeria de peças
Estudos de Caso
- Peças de metal automotivo
- Peças de máquinas
- Dissipador de calor LED
- Peças de Construção
- Peças Móveis
- Peças Médicas
- Partes eletrônicas
- Usinagem Sob Medida
- Peças de bicicleta
Lista de materiais
- Usinagem de Alumínio
- Usinagem de titânio
- Usinagem de aço inoxidável
- Usinagem de cobre
- Usinagem de latão
- Usinagem de Super Liga
- Peek Usinagem
- Usinagem UHMW
- Usinagem Unilate
- PA6 Usinagem
- Usinagem PPS
- Usinagem de Teflon
- Usinagem Inconel
- Usinagem de aço ferramenta
- Mais material
Galeria de peças