Como montar e instalar máquinas-ferramentas CNC da maneira certa e boas dicas
2023-10-30
Capítulo 1: Compreendendo as máquinas CNC
Neste capítulo, estabeleceremos as bases explorando o que são as máquinas CNC, os vários tipos disponíveis e os principais componentes que compõem uma máquina CNC.a. O que é uma máquina CNC?
Uma máquina CNC, abreviação de máquina de controle numérico computadorizado, é um equipamento sofisticado usado na fabricação e Processo de usinagemé. Ao contrário das máquinas convencionais operadas manualmente por operadores humanos, as máquinas CNC são automatizadas e controladas por computadores, permitindo operações precisas e altamente repetíveis. Essas máquinas são capazes de executar tarefas complexas, como cortar, furar, fresar e modelar materiais como metal, plástico, madeira e muito mais. No centro de uma máquina CNC está sua capacidade de interpretar e executar comandos de software de design auxiliado por computador (CAD) ou de fabricação auxiliada por computador (CAM). Este software gera uma série de códigos numéricos, muitas vezes chamados de códigos G e códigos M, que instruem a máquina CNC sobre como mover suas ferramentas de corte e peça de trabalho para alcançar o resultado desejado. As máquinas CNC revolucionaram as indústrias de manufatura, aumentando a eficiência, reduzindo erros humanos e permitindo a produção de componentes complexos e personalizados.b. Tipos de máquinas CNC
As máquinas CNC vêm em vários tipos, cada uma projetada para aplicações e indústrias específicas. Aqui estão alguns tipos comuns de máquinas CNC:- Fresagem CNC Máquinas: Essas máquinas são usadas para cortar e moldar materiais girando ferramentas de corte. Eles são amplamente empregados em indústrias como aeroespacial, automotiva e metalúrgica para tarefas como perfuração, fresagem e gravação.
- Tornos CNC: Os tornos CNC são projetados para girar a peça enquanto uma ferramenta de corte é usada para remover o material dela. Eles são essenciais para a fabricação de componentes cilíndricos, como eixoareia casquilhos.
- Roteadores CNC: Essas máquinas são usadas principalmente para cortar e modelar materiais como madeira, plástico e compósitos. Os roteadores CNC são comuns nas indústrias de marcenaria e sinalização.
- Cortadores de plasma CNC: Ideais para cortar chapas de metal, os cortadores de plasma CNC usam um jato de gás ionizado de alta velocidade para derreter e remover material. Eles são empregados na fabricação de metais e nas indústrias automotivas.
- Cortadores a laser CNC: As máquinas de corte a laser usam um feixe de laser de alta potência para cortar ou gravar com precisão vários materiais, incluindo metais, plásticos e têxteis. Eles encontram aplicações em indústrias que vão desde a fabricação de joias até a fabricação industrial.
- Cortadores CNC a jato de água: Os cortadores a jato de água usam um jato de água de alta pressão misturado com partículas abrasivas para cortar materiais. Eles são adequados para cortar uma ampla variedade de materiais, incluindo pedra, vidro e metais.
- Máquinas CNC EDM: As máquinas de usinagem por descarga elétrica (EDM) usam descargas elétricas para erodir o material da peça de trabalho. Eles são usados para tarefas complexas e de alta precisão, especialmente na fabricação de ferramentas e matrizes.
c. Componentes de uma máquina CNC
Compreender os componentes de uma máquina CNC é crucial para uma operação e manutenção eficazes. Aqui estão os principais componentes encontrados na maioria das máquinas CNC:- Estrutura da máquina: A estrutura da máquina fornece suporte estrutural para toda a máquina CNC. Normalmente é feito de materiais resistentes para garantir estabilidade e rigidez durante a operação.
- Fuso: O fuso é um componente motorizado responsável por segurar e girar ferramentas ou acessórios de corte. Ele desempenha um papel fundamental na precisão e velocidade do processo de usinagem.
- Sistema de eixo: As máquinas CNC operam ao longo de vários eixos, geralmente rotulados como X, Y e Z. Esses eixos definem o movimento da máquina no espaço tridimensional. Algumas máquinas podem ter eixos rotacionais adicionais, como A, B e C, para operações mais complexas.
- Trocador de ferramentas: Muitas máquinas CNC são equipadas com trocadores automáticos de ferramentas que permitem a troca rápida de ferramentas de corte durante um processo de usinagem. Isso melhora a eficiência e reduz o tempo de inatividade.
- Painel de controle: O painel de controle contém a interface através da qual os operadores ou programadores podem inserir comandos, carregar programas e monitorar o status da máquina.
- Mesa de trabalho ou sistema de fixação: A mesa de trabalho é onde a peça de trabalho é mantida firmemente no lugar durante a usinagem. Vários dispositivos de fixação, como grampos, tornos e luminárias, são usados para garantir que a peça de trabalho permaneça estável e posicionada corretamente.
- Sistema de direção: O sistema de acionamento é composto por motores e atuadores responsáveis por movimentar os componentes da máquina ao longo dos eixos especificados. O controle preciso do sistema de acionamento é essencial para uma usinagem precisa.
- Sistema de refrigeração: O resfriamento é vital durante Usinagem Cnc Multi Eixo para evitar o superaquecimento de ferramentas e peças de trabalho. As máquinas CNC geralmente possuem um sistema de refrigeração para manter a temperatura ideal.
- Computador de controle: O computador de controle abriga o hardware e software necessários para operar a máquina CNC. Ele interpreta os códigos G e códigos M gerados pelo software CAD/CAM e os converte em movimentos e ações.
Capítulo 2: Preparação Pré-Instalação
Antes de iniciar a instalação de sua máquina CNC, é fundamental fazer uma preparação minuciosa. Este capítulo irá guiá-lo através das considerações essenciais de pré-instalação, incluindo configuração do espaço de trabalho, requisitos de energia e elétricos e medidas de segurança para garantir um processo de instalação tranquilo e seguro.a. Considerações sobre o espaço de trabalho
- Requisitos de espaço: Comece avaliando o espaço disponível em sua oficina ou instalação. Certifique-se de que a área seja espaçosa o suficiente para acomodar sua máquina CNC, incluindo espaço suficiente para acesso e manutenção seguros. Considere as dimensões da máquina, o espaço necessário para o manuseio de materiais e quaisquer equipamentos ou estações de trabalho adicionais.
- Ventilação: A ventilação adequada é crucial para dissipar o calor gerado durante a usinagem e para remover quaisquer vapores ou partículas de poeira potencialmente prejudiciais. Instale sistemas de ventilação adequados ou equipamentos de filtragem de ar conforme necessário para manter um ambiente de trabalho limpo e seguro.
- Pisos: Certifique-se de que o piso da área designada esteja nivelado, estável e capaz de suportar o peso da máquina CNC. Pisos irregulares ou fracos podem causar vibrações e imprecisões na máquina durante a operação.
- Acessibilidade: Planeje o acesso fácil à máquina CNC para instalação, manutenção e reparo. Certifique-se de que haja caminhos desobstruídos e espaço suficiente para manobrar máquinas e materiais pesados.
- Iluminação: A iluminação adequada é essencial para uma operação segura e precisa. Certifique-se de que o espaço de trabalho esteja bem iluminado para evitar acidentes e fornecer visibilidade clara do processo de usinagem.
b. Requisitos de energia e elétricos
- Fonte elétrica: Determine os requisitos elétricos específicos de sua máquina CNC. Verifique as especificações técnicas da máquina e consulte o fabricante ou fornecedor para garantir que a alimentação elétrica da sua instalação atenda a esses requisitos.
- Tensão e Fase: Máquinas CNC podem exigir diferentes níveis de tensão (por exemplo, 110V, 220V, 440V) e fases (monofásica ou trifásica). Certifique-se de que a alimentação elétrica corresponda às especificações da máquina.
- Painel elétrico: Instale um painel elétrico dedicado para a máquina CNC para evitar sobrecarregar os circuitos existentes. Contrate um eletricista licenciado para cuidar da fiação e das conexões profissionalmente.
- Proteção contra surtos: Invista em dispositivos de proteção contra surtos para proteger os componentes eletrônicos sensíveis da máquina CNC contra flutuações de tensão e surtos elétricos.
- Aterramento: Garanta o aterramento adequado da máquina CNC e do sistema elétrico para mitigar o risco de riscos elétricos e danos ao equipamento.
c. Medidas de segurança
- Equipamento de segurança: Priorize a segurança fornecendo equipamentos de proteção individual (EPI) adequados para operadores e técnicos. Isso pode incluir óculos de segurança, proteção auditiva, luvas e roupas de proteção.
- Procedimentos de emergência: Desenvolva e documente procedimentos de desligamento de emergência que possam parar rapidamente a máquina CNC em caso de eventos imprevistos ou acidentes. Certifique-se de que todo o pessoal seja treinado nesses procedimentos.
- Segurança contra incêndios: Instale extintores de incêndio e detectores de fumaça nas proximidades da máquina CNC. Implemente protocolos de segurança contra incêndio, como manter materiais inflamáveis longe da máquina e manter um plano de saída de incêndio.
- Bloqueio/Etiquetagem (LOTO): Implemente procedimentos LOTO para evitar a partida acidental da máquina durante a manutenção ou reparo. Use cadeados e etiquetas para indicar quando uma máquina está em manutenção.
- Treinamento de segurança: Conduza treinamento de segurança abrangente para todo o pessoal que irá operar, manter ou trabalhar próximo à máquina CNC. Enfatize as práticas seguras e a importância de seguir os protocolos de segurança.
- Primeiros socorros: Mantenha um kit de primeiros socorros bem abastecido nas proximidades da máquina CNC. Certifique-se de que pessoal treinado esteja disponível para prestar primeiros socorros imediatos em caso de ferimentos.
Capítulo 3: Montagem da Máquina CNC
Depois de concluir os preparativos de pré-instalação, é hora de passar para a fase de montagem. Neste capítulo, forneceremos um guia passo a passo sobre a montagem de sua máquina CNC, abrangendo tarefas essenciais, desde a desembalagem e inspeção até o gerenciamento de cabos.a. Desembalagem e inspeção
- unboxing: Comece desempacotando cuidadosamente todos os componentes da sua máquina CNC. Siga as instruções do fabricante ao desembalar para evitar danos durante o processo. Use ferramentas e equipamentos de elevação apropriados, se necessário.
- Inventário de Componentes: Crie uma lista de verificação de inventário para garantir que você recebeu todos os componentes listados no manual ou na documentação da máquina. Verifique se nada está faltando ou danificado.
- Inspecione quanto a danos: Examine cada componente cuidadosamente em busca de sinais de danos, como amassados, arranhões ou peças dobradas. Documente quaisquer problemas e notifique o fabricante ou fornecedor imediatamente.
b. Organizando Componentes
- Organizar área de trabalho: Antes da montagem, certifique-se de que seu espaço de trabalho esteja limpo e bem organizado. Limpe qualquer desordem e forneça amplo espaço para dispor e organizar os componentes.
- Agrupar peças semelhantes: Agrupe peças semelhantes para facilitar o processo de montagem. Componentes como prendedorItens, suportes e ferragens devem ser organizados em recipientes ou bandejas separadas para fácil acesso.
- Consulte os manuais: Revise os manuais de montagem e a documentação fornecida pelo fabricante. Familiarize-se com as etapas de montagem, diagramas e quaisquer instruções específicas.
c. Montagem da estrutura da máquina
- Montagem da Base: Comece com a base da máquina CNC. Siga as instruções do fabricante para montar a estrutura base com segurança. Certifique-se de que esteja nivelado e estável.
- Colunas e Estruturas de Apoio: Monte as colunas e estruturas de suporte, alinhando-as com precisão com a base. Aperte todos os parafusos e fixadores com os valores de torque recomendados.
- Guias e trilhos: Instale as guias e trilhos que guiarão o movimento dos componentes de corte ou de fixação da ferramenta da máquina. Certifique-se de que estejam devidamente alinhados e fixados com segurança.
d. Anexando motores e drives
- Instalação do motor: Monte os motores nas posições designadas de acordo com as instruções do fabricante. Certifique-se de que os motores estejam firmemente fixados e alinhados com os mecanismos de acionamento.
- Sistema de direção: Conecte os motores aos mecanismos de acionamento usando acoplamentos ou correias apropriadas. Garanta a tensão e o alinhamento adequados para evitar folgas e imprecisões.
e. Instalando o Painel de Controle
- Montagem do painel de controle: Instale o painel de controle em um local conveniente, geralmente de fácil acesso ao operador. Certifique-se de que ele esteja montado e posicionado com segurança para obter visibilidade e acessibilidade ideais.
- Conexões elétricas: Conecte o painel de controle ao sistema elétrico da máquina seguindo os esquemas elétricos fornecidos na documentação do fabricante. Verifique novamente todas as conexões quanto à precisão.
f. Gerenciamento de cabos
- Roteamento de cabo: Encaminhe cuidadosamente todos os cabos, fios e mangueiras de maneira organizada para evitar emaranhados ou interferências com peças móveis. Use bandejas de cabos ou clipes para fixar e proteger os cabos.
- Marcação: Rotule cabos e fios com marcadores ou etiquetas de identificação para simplificar a solução de problemas e a manutenção. Marque claramente a finalidade e o destino de cada cabo.
- Teste: Antes de fechar qualquer gabinete ou painel, realize um teste preliminar para garantir que todas as conexões elétricas estejam funcionando corretamente. Verifique se os motores e sensores respondem conforme o esperado.
Capítulo 4: Alinhamento e Nivelamento
No Capítulo 4, nos aprofundaremos no processo crítico de alinhamento e nivelamento de sua máquina CNC. O alinhamento e nivelamento adequados são fundamentais para garantir a exatidão e precisão das operações da sua máquina. Este capítulo aborda a importância do alinhamento e nivelamento, as ferramentas e equipamentos necessários e um guia passo a passo para o processo de alinhamento e nivelamento.a. Importância do Alinhamento e Nivelamento
- Exatidão e precisão: O alinhamento e o nivelamento são essenciais para atingir o alto grau de exatidão e precisão exigido na usinagem CNC. O desalinhamento ou irregularidade pode levar a erros dimensionais nas peças acabadas.
- Desgaste reduzido e desgaste: O alinhamento adequado reduz o estresse desnecessário nos componentes da máquina, como rolamentose guias. Isto prolonga a vida útil da máquina e reduz os custos de manutenção.
- Vibração minimizada: Uma máquina bem alinhada e nivelada gera menos vibrações, resultando em melhores acabamentos superficiais e menor desgaste da ferramenta. As vibrações também podem afetar a longevidade de componentes eletrônicos sensíveis.
- Segurança: Máquinas desalinhadas ou desniveladas podem representar riscos à segurança. Por exemplo, uma máquina que não esteja nivelada pode tombar ou mover-se inesperadamente durante a operação.
b. Ferramentas e equipamentos necessários
Para realizar o alinhamento e nivelamento corretamente, serão necessárias as seguintes ferramentas e equipamentos:- Níveis de precisão: Níveis de precisão de alta qualidade são cruciais para medir com precisão o alinhamento e nivelamento da máquina.
- Ferramentas de ajuste: Dependendo do projeto da sua máquina, você pode precisar de ferramentas específicas, como chaves inglesas, calços ou parafusos de ajuste.
- Indicadores de discagem: Os relógios comparadores ajudam a medir o alinhamento de vários componentes da máquina, incluindo o fuso da ferramenta e a mesa de trabalho.
- Medidores de folga: Os calibradores de folga são usados para medir folgas e folgas entre os componentes da máquina durante o alinhamento.
- Laser de alinhamento: Um laser de alinhamento pode ser útil para avaliar a retilineidade de guias e outros componentes lineares.
c. Processo passo a passo de alinhamento e nivelamento
Siga estas etapas para alinhar e nivelar sua máquina CNC:Etapa 1: preparar o espaço de trabalho
Certifique-se de que o espaço de trabalho esteja limpo, livre de detritos e bem iluminado. Remova quaisquer obstáculos que possam dificultar o processo de alinhamento e nivelamento.Passo 2: Estabelecimento do Ponto de Referência
Selecione um ponto de referência estável na estrutura ou base da máquina, geralmente fornecido pelo fabricante. Este ponto servirá como referência inicial para todas as medições.Etapa 3: nivelar a máquina
- Coloque níveis de precisão em diversas superfícies da máquina, como base, colunas e mesa de trabalho.
- Ajuste os parafusos ou calços de nivelamento conforme necessário para obter um alinhamento horizontal perfeito. Verifique a precisão dos indicadores de bolha nos níveis.
Etapa 4: Alinhamento de guias e slides
- Use relógios comparadores e lasers de alinhamento para verificar a retilineidade e o paralelismo de guias, corrediças e outros componentes lineares.
- Ajuste os componentes apropriados para corrigir qualquer desalinhamento detectado.
Passo 5: Alinhamento do Fuso
- Monte um relógio comparador no fuso da máquina ou no porta-ferramentas.
- Gire o fuso para verificar a excentricidade e a concentricidade. Ajuste o fuso conforme necessário para minimizar o desvio.
Etapa 6: Alinhamento da mesa de trabalho
- Verifique o alinhamento da mesa de trabalho ou dispositivo de fixação usando relógios comparadores.
- Ajuste o posicionamento da mesa de trabalho para garantir que esteja perpendicular aos eixos da máquina.
- Após os ajustes, verifique novamente todos os alinhamentos para garantir que atendam às tolerâncias especificadas.
- Realize testes para verificar se a máquina opera com precisão e produz os resultados desejados.
Etapa 8: Documentação
Mantenha registros detalhados do processo de alinhamento e nivelamento, incluindo medições, ajustes feitos e quaisquer problemas encontrados. Esta documentação será valiosa para referência e manutenção futuras.Etapa 9: Inspeção Final e Certificação
Considere contratar um técnico ou engenheiro qualificado para realizar uma inspeção final e certificação para garantir que a máquina CNC atenda aos padrões da indústria e aos requisitos de segurança. O alinhamento e o nivelamento adequados são essenciais para a operação confiável e precisa de sua máquina CNC. Não tenha pressa durante esse processo, pois a precisão é fundamental. Seguindo essas etapas e usando as ferramentas certas, você pode garantir que sua máquina esteja em condições ideais para operações de usinagem bem-sucedidas. No próximo capítulo, exploraremos os requisitos de fiação elétrica para sua máquina CNC.Capítulo 5: Fiação Elétrica
Neste capítulo, nos aprofundaremos nos aspectos de fiação elétrica da instalação de sua máquina CNC. A fiação elétrica adequada é crucial para a operação segura e eficiente da máquina. Este capítulo aborda a compreensão dos sistemas elétricos, a fiação da máquina CNC e importantes precauções de segurança.a. Compreendendo os sistemas elétricos
- Fonte de energia: As máquinas CNC requerem uma fonte de alimentação estável e adequada. Entenda os requisitos de tensão, frequência e fase especificados pelo fabricante da máquina. Certifique-se de que a fonte de alimentação seja confiável e tenha capacidade adequada para suportar a carga elétrica da máquina.
- Painel elétrico: A maioria das máquinas CNC possui um painel elétrico que abriga vários componentes, incluindo disjuntores, relés, contatores e blocos de terminais. Familiarize-se com os componentes do painel e suas funções.
- Diagramas de fiação: Revise os diagramas de fiação fornecidos pelo fabricante da máquina. Estes diagramas ilustram as conexões entre os componentes e são essenciais para a fiação correta.
- Aterramento: O aterramento adequado é fundamental para a segurança. Certifique-se de que a máquina e o sistema elétrico estejam aterrados de acordo com os códigos elétricos locais e as recomendações do fabricante.
b. Fiação da máquina CNC
Siga estas etapas para conectar sua máquina CNC:Passo 1: Desligar
Certifique-se de que a máquina e a fonte de alimentação estejam desligadas antes de iniciar qualquer trabalho de fiação. Desconecte a máquina da fonte de alimentação.Etapa 2: Plano de fiação
Crie um plano de fiação com base nos diagramas de fiação do fabricante. Identifique os componentes, como motores, sensores, interruptores e painel de controle, e determine suas interconexões.Etapa 3: Seleção do Cabo
Use cabos e fios apropriados que atendam aos requisitos de tensão e corrente da máquina. Certifique-se de que os cabos tenham a bitola e o tipo de isolamento corretos.Etapa 4: roteamento de cabos
Passe cuidadosamente os cabos e fios ao longo das bandejas de cabos ou conduítes da máquina. Mantenha-os organizados e separados dos componentes móveis para evitar danos.Etapa 5: conexões de terminal
Conecte os fios aos terminais apropriados em componentes como motores, sensores e interruptores. Garanta conexões seguras por crimpagem ou soldagem conforme necessário. Use etiquetas de fios para fácil identificação.Etapa 6: Fiação do Painel de Controle
Dentro do painel de controle, conecte os fios aos respectivos blocos de terminais, disjuntores, contatores e relés conforme especificado nos diagramas de fiação. Seja meticuloso em seu trabalho para evitar conexões cruzadas ou fios soltos.Etapa 7: Conexão da fonte de alimentação
Conecte a máquina à fonte de alimentação seguindo as orientações do fabricante. Verifique novamente as configurações de tensão, fase e frequência para garantir que correspondam aos requisitos da máquina.Etapa 8: Medidas de Segurança
Implemente recursos de segurança, como interruptores de parada de emergência e intertravamentos de segurança, conforme necessário. Certifique-se de que esses dispositivos de segurança estejam conectados corretamente e testados quanto à funcionalidade.Etapa 9: teste
Antes de fechar o painel de controle e ligar a máquina, realize um teste de continuidade para verificar falhas na fiação ou curtos-circuitos. Certifique-se de que todas as conexões estejam seguras e livres de fios soltos.c. Precauções de segurança
- Bloqueio/Etiquetagem (LOTO): Implemente procedimentos LOTO para evitar a partida acidental da máquina durante atividades de fiação ou manutenção. Dispositivos de bloqueio devem ser usados para isolar fontes de energia.
- Eletricista qualificado: O trabalho elétrico deve ser executado por um eletricista ou técnico qualificado que conheça os requisitos elétricos da máquina e os códigos elétricos locais.
- Proteção de sobrecarga: Instale dispositivos adequados de proteção contra sobrecarga, como disjuntores ou fusíveis, para evitar danos em caso de falhas elétricas.
- Aterramento: Certifique-se de que a máquina e todos os componentes elétricos estejam devidamente aterrados para evitar riscos elétricos.
- Marcação: Identifique claramente todos os fios, cabos e componentes para facilitar a solução de problemas e manutenção futura.
- Inspeções Regulares: Inspecione periodicamente o sistema elétrico em busca de sinais de desgaste, danos ou conexões soltas. Resolva quaisquer problemas imediatamente.
- Procedimentos de emergência: Estabelecer e comunicar procedimentos de emergência para problemas elétricos, incluindo incêndios elétricos ou incidentes com choques elétricos.
Capítulo 6: Instalando o Software de Controle
Neste capítulo, exploraremos o processo de instalação do software de controle para sua máquina CNC. O software de controle é o cérebro do seu sistema CNC, responsável por interpretar e executar as instruções de usinagem. Este capítulo cobre uma visão geral do software de controle de máquina CNC, um guia passo a passo para instalação do software e os procedimentos de calibração e teste.a. Visão geral do software de controle de máquina CNC
- Papel do software de controle: O software de controle de máquina CNC é responsável por traduzir os dados de projeto e percurso da ferramenta do software CAD/CAM em movimentos específicos da máquina. Gera os códigos G e códigos M que comandam os motores e atuadores da máquina.
- Tipos de software de controle: Existem vários tipos de software de controle CNC, desde software proprietário fornecido por fabricantes de máquinas até soluções de código aberto e de terceiros. Escolha um software que atenda aos requisitos da sua máquina e à sua familiaridade com sua interface.
- Características: O software de controle pode variar em termos de recursos e capacidades. Procure um software que ofereça as funcionalidades necessárias para suas necessidades específicas de usinagem, como geração de percursos, troca de ferramentas e controle de velocidade do fuso.
b. Instalação passo a passo do software
Siga estas etapas para instalar o software de controle para sua máquina CNC:Etapa 1: Requisitos do sistema
Verifique os requisitos do sistema especificados pelo fabricante do software de controle. Certifique-se de que seu computador atenda a esses requisitos em termos de hardware, sistema operacional e memória disponível.Etapa 2: download de software ou mídia de instalação
Obtenha o software de controle baixando-o do site do fabricante ou usando a mídia de instalação fornecida pelo fabricante.Etapa 3: Instalação
- Clique duas vezes no arquivo de instalação do software para iniciar o processo de instalação.
- Siga as instruções na tela fornecidas pelo instalador. Isso pode incluir a seleção de diretórios de instalação, a aceitação de contratos de licença e a definição de configurações de software.
- Certifique-se de que a instalação foi bem-sucedida e que nenhum erro foi encontrado.
Etapa 4: licenciamento e ativação
Se o software de controle exigir licenciamento ou ativação, siga as orientações do fabricante para concluir esse processo. Certifique-se de ter as chaves de licença ou códigos de ativação necessários.Etapa 5: configuração da máquina
Configure o software de controle para corresponder às especificações da sua máquina CNC. Isto pode envolver a definição de parâmetros para os eixos da máquina, tipos de motores e outros componentes de hardware.Etapa 6: Banco de dados de ferramentas e materiais
Crie ou importe um banco de dados de ferramentas e materiais para o software de controle. Esta informação é crucial para a geração do percurso e seleção dos parâmetros de usinagem apropriados.c. Calibração e Teste
Após a instalação do software de controle, siga estas etapas para calibração e teste:Etapa 1: Homing e configuração do ponto de referência
- Coloque a máquina na posição inicial movendo todos os eixos para suas posições de referência ou iniciais. Isto estabelece um ponto de partida conhecido para os movimentos da máquina.
- Verifique se a máquina retorna à posição de referência com precisão.
Passo 2: Calibração da Ferramenta
- Calibre o comprimento e o diâmetro da ferramenta. Isso garante que a máquina conheça as dimensões exatas das ferramentas que utilizará.
- Execute cortes de teste ou rotinas de toque de ferramenta para validar a calibração da ferramenta.
Etapa 3: configuração da peça de trabalho
- Prenda uma peça ou material de teste na mesa de trabalho ou no sistema de fixação da máquina.
- Certifique-se de que a peça de trabalho esteja devidamente alinhada e fixada.
Etapa 4: execuções de teste
- Carregue um programa de teste simples no software de controle.
- Execute o programa de teste para observar os movimentos da máquina e os resultados de usinagem.
- Verifique se há problemas como movimentos inesperados, colisões de ferramentas ou imprecisões.
Etapa 5: ajuste fino
Se forem identificados problemas durante o teste, ajuste as configurações do software de controle, os deslocamentos da ferramenta ou a configuração da peça conforme necessário. Repita os testes até que a máquina funcione de forma precisa e confiável.Etapa 6: Documentação
Documente todos os resultados de calibração e testes, incluindo quaisquer ajustes feitos no software de controle. Esta documentação é valiosa para referência futura e solução de problemas. A instalação do software de controle é uma etapa crucial no processo de configuração da máquina CNC. Seguindo as instruções do fabricante, calibrando a máquina e realizando testes completos, você pode garantir que sua máquina CNC esteja pronta para produção e seja capaz de produzir resultados precisos e exatos. No próximo capítulo, exploraremos a importância da lubrificação e manutenção para manter o desempenho e a longevidade de sua máquina CNC.Capítulo 7: Lubrificação e Manutenção
Neste capítulo, focaremos nos aspectos críticos de lubrificação e manutenção de sua máquina CNC. A lubrificação adequada e a manutenção regular são essenciais para garantir a longevidade, precisão e confiabilidade do seu equipamento CNC. Abordaremos a importância da lubrificação, dos pontos de lubrificação e do estabelecimento de um cronograma de manutenção.a. Por que a lubrificação é importante
A lubrificação desempenha um papel vital no desempenho e na longevidade da sua máquina CNC por vários motivos:- Redução de Fricção: A lubrificação reduz o atrito entre as peças móveis, como rolamentos, guias e fusos de esferas. Isso minimiza o desgaste dos componentes, prolongando sua vida útil.
- Dissipação de calor: Os lubrificantes dissipam o calor gerado durante a usinagem, evitando o superaquecimento de componentes críticos. Isto ajuda a manter a precisão dimensional e reduz o risco de expansão térmica.
- Operação suave: A lubrificação adequada garante movimentos mais suaves e precisos dos componentes da máquina. Isto é essencial para alcançar a alta precisão exigida na usinagem CNC.
- Prevenindo a corrosão: Os lubrificantes fornecem uma barreira protetora contra umidade e contaminantes, reduzindo o risco de corrosão em superfícies metálicas.
- Redução de ruído: A lubrificação pode reduzir o ruído gerado durante a operação da máquina, criando um ambiente de trabalho mais silencioso e confortável.
b. Pontos de lubrificação
Diferentes máquinas CNC possuem vários pontos de lubrificação que requerem atenção. Aqui estão alguns pontos comuns de lubrificação a serem considerados:- Guias Lineares: Aplique lubrificante nas guias lineares, que facilitam a movimentação dos eixos da máquina. Isso pode incluir parafusos de esferas, rolamentos lineares e guias deslizantes.
- Rolamentos do eixo: Lubrifique os rolamentos do fuso para garantir uma rotação suave e reduzir o atrito durante as operações de corte ou usinagem.
- Mecanismo de troca de ferramentas: Se a sua máquina possuir um trocador automático de ferramentas, certifique-se de que as partes móveis do mecanismo estejam adequadamente lubrificadas para evitar travamentos ou mau funcionamento.
- Caixas de câmbio: As caixas de engrenagens, se presentes na sua máquina, podem exigir lubrificação em intervalos especificados para manter a eficiência e reduzir o desgaste.
- Parafusos de esfera: Os fusos de esferas são componentes cruciais em máquinas CNC. A lubrificação adequada dos fusos de esferas e seus componentes associados é essencial para posicionamento e movimento precisos.
- Bomba de refrigeração: Se a sua máquina utilizar um sistema de refrigeração, certifique-se de que a bomba esteja devidamente lubrificada e que o líquido refrigerante esteja limpo e livre de contaminantes.
- Motores de eixo: Dependendo do tipo de motor utilizado para movimentação do eixo (por exemplo, passo a passo ou servo), siga as recomendações do fabricante para lubrificação ou manutenção.
- Selos e juntas: Inspecione e substitua vedações e juntas desgastadas ou danificadas conforme necessário para evitar vazamento e contaminação de lubrificante.
c. Cronograma de manutenção
Estabelecer um cronograma de manutenção regular é essencial para manter sua máquina CNC em ótimas condições. Aqui estão as etapas para criar um cronograma de manutenção:Etapa 1: Diretrizes do Fabricante
Consulte a documentação e recomendações do fabricante para intervalos de manutenção, tipos de lubrificação e procedimentos específicos.Passo 2: Manutenção Diária
Implemente rotinas de manutenção diária que incluam tarefas como remoção de detritos, verificação de fixadores soltos e inspeção dos níveis de líquido refrigerante. Essas tarefas ajudam a evitar o agravamento de problemas menores.Etapa 3: Manutenção Semanal ou Mensal
Agende tarefas de manutenção mais aprofundadas semanalmente ou mensalmente, dependendo do uso da sua máquina. Isso pode envolver limpeza, lubrificação e inspeções completas de componentes críticos.Etapa 4: Manutenção Trimestral ou Semestral
Execute tarefas de manutenção mais extensas, como verificação e ajuste de alinhamento, inspeção de conexões elétricas e substituição de peças desgastadas ou danificadas.Etapa 5: Manutenção Anual
Anualmente, considere uma inspeção abrangente por um técnico ou engenheiro qualificado. Isto deve incluir um ciclo completo de lubrificação, verificações de calibração e quaisquer reparos ou substituições necessários.Etapa 6: Documentação
Mantenha registros detalhados de todas as atividades de manutenção, incluindo datas, tarefas executadas e quaisquer problemas identificados. Esta documentação é inestimável para rastrear o histórico da máquina e planejar manutenções futuras.Etapa 7: treinamento
Certifique-se de que o pessoal responsável pela manutenção seja adequadamente treinado e tenha acesso às ferramentas e recursos necessários. A lubrificação e a manutenção regulares são essenciais para maximizar a vida útil e o desempenho da sua máquina CNC. Seguindo um cronograma de manutenção bem estabelecido e abordando os pontos de lubrificação, você pode evitar o desgaste prematuro e garantir que sua máquina continue a produzir peças precisas e de alta qualidade. No próximo capítulo, discutiremos procedimentos e diretrizes de segurança para operar sua máquina CNC.Capítulo 8: Procedimentos de Segurança para Máquinas CNC
A segurança é de suma importância ao trabalhar com máquinas CNC. Neste capítulo, exploraremos os principais procedimentos e diretrizes de segurança para a operação de máquinas CNC, incluindo segurança de máquinas CNC, procedimentos de desligamento de emergência e uso de equipamentos de proteção individual (EPI).a. Segurança de máquinas CNC
- Treinamento: Certifique-se de que todo o pessoal que opera ou trabalha próximo a máquinas CNC recebeu treinamento abrangente de segurança. Isto deve incluir treinamento específico da máquina, procedimentos operacionais seguros e reconhecimento de perigos.
- Protetores de máquinas: Mantenha todas as proteções da máquina e intertravamentos de segurança no lugar e funcionando corretamente. Esses recursos de segurança foram projetados para proteger os operadores contra peças móveis e perigos potenciais.
- Etiquetas de segurança: Certifique-se de que as etiquetas de segurança e os sinais de alerta estejam exibidos de forma destacada na máquina. Esses rótulos fornecem informações essenciais sobre perigos potenciais e precauções de segurança.
- Parada de emergência: Familiarize os operadores com a localização e uso do botão de parada de emergência. Certifique-se de que seja facilmente acessível em caso de emergência.
- Área de trabalho limpa: Mantenha um espaço de trabalho organizado ao redor da máquina CNC. Remova quaisquer ferramentas, materiais ou detritos desnecessários que possam representar risco de tropeçar ou interferir na operação da máquina.
- Bloqueio/etiquetagem da máquina (LOTO): Implemente procedimentos de bloqueio/sinalização para desenergizar e proteger a máquina antes de realizar manutenção ou reparos. Dispositivos de bloqueio evitam a inicialização acidental da máquina.
- Segurança do fuso e da ferramenta: Manuseie as ferramentas de corte e as trocas de ferramentas com cuidado. Certifique-se de que as ferramentas estejam devidamente fixadas nos porta-ferramentas e que as trocas de ferramentas sejam realizadas seguindo procedimentos seguros.
- Manuseio de materiais: Use equipamentos e técnicas de elevação apropriados ao manusear materiais pesados ou peças de trabalho. Evite sobrecarregar a capacidade de peso da máquina.
- Segurança contra incêndios: Mantenha extintores de incêndio e detectores de fumaça por perto. Desenvolver e comunicar protocolos de segurança contra incêndio, incluindo a localização de saídas de incêndio e procedimentos de evacuação.
b. Procedimentos de desligamento de emergência
- Botão de parada de emergência: Em caso de emergência ou quando for necessário o desligamento imediato, pressione o botão de parada de emergência. Este botão normalmente é grande, vermelho e facilmente acessível.
- Pare todo o movimento: O botão de parada de emergência deve interromper todos os movimentos da máquina e desligar a energia da máquina. Certifique-se de que a máquina pare completamente.
- Bloqueio/Sinalização: Depois de usar o botão de parada de emergência, siga os procedimentos de bloqueio/sinalização para proteger a máquina e evitar reinicializações acidentais.
- Notificar as autoridades: Se ocorrer um acidente ou situação perigosa, entre em contato com as autoridades apropriadas, como pessoal de manutenção ou supervisores, para resolver o problema e garantir que a máquina possa ser operada novamente com segurança.
c. Equipamento de Proteção Individual (EPI)
- Óculos de segurança: Os operadores e o pessoal nas proximidades da máquina CNC devem usar óculos de segurança com resistência adequada ao impacto para proteger os olhos de detritos projetados.
- Proteção auditiva: Em oficinas mecânicas barulhentas, deve-se usar proteção auditiva, como protetores auriculares ou protetores auriculares, para evitar danos auditivos.
- Luvas: Ao manusear materiais ou realizar tarefas de manutenção, use luvas adequadas ao trabalho. Certifique-se de que as luvas não representam um risco perto de peças móveis da máquina.
- Proteção respiratória: If material de usinagemSe gerar poeira ou fumaça, use equipamento de proteção respiratória, como máscaras contra poeira ou respiradores, para proteção contra riscos de inalação.
- Sapatos de segurança: Use sapatos de segurança resistentes ou botas com sola antiderrapante para proteger contra lesões nos pés e garantir uma boa tração no espaço de trabalho.
- Roupa de proteção: Dependendo do processo de usinagem e dos materiais utilizados, use roupas de proteção adequadas, como aventais ou macacões de corpo inteiro.
- Capacetes de segurança: Em ambientes onde a queda de objetos representa um risco, use capacetes de segurança ou capacetes para proteção da cabeça.
- Protetores faciais: Para tarefas que envolvam riscos potenciais para o rosto, como respingos de líquido refrigerante ou lascas, use protetores faciais além dos óculos de segurança.
Capítulo 9: Solução de problemas comuns de instalação
Neste capítulo, exploraremos problemas comuns que podem surgir durante a instalação de máquinas CNC e forneceremos soluções para resolver esses problemas. Além disso, discutiremos técnicas de solução de problemas que podem ajudá-lo a identificar e resolver problemas de maneira eficaz.a. Problemas e soluções comuns
-
Problemas elétricos:
- Problema: A máquina CNC não liga.
- Alternativa? Verifique a fonte de alimentação, as conexões elétricas e os fusíveis. Certifique-se de que o botão de parada de emergência esteja liberado.
-
Desalinhamento Mecânico:
- Problema: A máquina produz cortes ou dimensões da peça imprecisas.
- Alternativa? Realinhe e nivele a máquina. Verifique se há componentes soltos ou guias desgastadas e substitua conforme necessário.
-
Vibração ou vibração da ferramenta:
- Problema: A máquina produz vibrações ou vibração da ferramenta, afetando o acabamento superficial.
- Alternativa? Verifique o porta-ferramenta e a pinça do fuso quanto ao assentamento adequado. Ajuste os parâmetros de corte e as configurações do percurso.
-
Erros de comunicação:
- Problema: O controlador CNC não pode se comunicar com o computador ou software CAD/CAM.
- Alternativa? Verifique as conexões dos cabos, as taxas de transmissão e as configurações na máquina e no computador. Garanta instalações adequadas de software e driver.
-
Quebra de ferramenta:
- Problema: As ferramentas freqüentemente quebram durante a usinagem.
- Alternativa? Verifique o alinhamento da ferramenta, a condição do porta-ferramenta e a excentricidade do fuso. Ajuste os avanços e velocidades com base no material da ferramenta e na peça de trabalho.
-
Problemas de refrigerante ou lubrificação:
- Problema: Fluxo de líquido refrigerante/lubrificação insuficiente ou irregular.
- Alternativa? Verifique os componentes do sistema de refrigeração e lubrificação, como bombas, mangueiras e bicos. Limpe ou substitua os filtros e garanta os níveis adequados de fluido.
-
Erros de software:
- Problema: O software de controle exibe mensagens de erro ou comportamento inesperado.
- Alternativa? Revise as mensagens de erro e consulte a documentação do software. Verifique se há problemas de compatibilidade e atualize o software ou firmware conforme necessário.
b. Técnicas de solução de problemas
- Abordagem Sistemática: Ao solucionar problemas, adote uma abordagem sistemática, identificando e isolando a origem do problema. Comece com as verificações mais simples e investigue progressivamente as causas mais complexas.
- Documentação: Consulte os manuais da máquina, a documentação e os recursos fornecidos pelo fabricante para obter orientação sobre solução de problemas e interpretações de códigos de erro.
- Medição e Teste: Use instrumentos de medição como relógios comparadores, paquímetros e micrômetros para avaliar o alinhamento, as dimensões e o desvio da ferramenta. Realize cortes de teste para verificar a precisão da usinagem.
- Inspeção visual: Faça uma inspeção visual completa da máquina, verificando se há fixadores soltos, componentes danificados ou sinais visíveis de desgaste.
- Registros e Registros: Revise logs de manutenção, logs de erros e registros de problemas anteriores para identificar problemas ou padrões recorrentes.
- Consulte Especialistas: Se você encontrar problemas complexos ou persistentes, consulte especialistas, como suporte técnico do fabricante, técnicos qualificados ou maquinistas experientes que possam ter encontrado problemas semelhantes.
- Solução de problemas segura: Sempre garanta a segurança durante a solução de problemas. Siga os procedimentos de bloqueio/sinalização, desligue a máquina e use equipamento de proteção individual (EPI) apropriado.
- Documentação: Mantenha registros detalhados das atividades de solução de problemas, incluindo as etapas executadas, as observações e as resoluções aplicadas. Esses registros podem ser valiosos para referência futura.
- Aprendizado contínuo: Incentive uma cultura de aprendizado contínuo e compartilhamento de conhecimento entre sua equipe. A experiência adquirida com a solução de problemas pode levar a melhores práticas de manutenção preventiva.
Capítulo 10: Verificações e testes finais
Neste capítulo final, discutiremos as etapas essenciais para executar programas de teste, garantir a precisão e ajustar a instalação de sua máquina CNC para alcançar o desempenho ideal.a. Executando programas de teste
- Seleção de programas de teste: Prepare programas de teste que abrangem uma variedade de operações de usinagem que sua máquina CNC executará. Esses programas devem incluir movimentos básicos, trocas de ferramentas e vários cenários de corte.
- Configuração de ferramenta e peça de trabalho: Monte as ferramentas apropriadas e fixe uma peça de teste na mesa de trabalho ou acessório da máquina. Certifique-se de que os deslocamentos da ferramenta e de trabalho estejam programados corretamente.
- Funcionamento a seco: Inicialmente, faça um ensaio sem qualquer corte. Isso permite verificar os movimentos da máquina, as trocas de ferramentas e o fluxo geral do programa em busca de erros ou comportamentos inesperados.
- Seleção de Material: Escolha um material de teste semelhante ao que você planeja usar em seus projetos de usinagem reais. Isso garante que os resultados do teste imitem de perto as condições do mundo real.
- Testes de corte: Execute os programas de teste com operações de corte. Monitore o desempenho da máquina, prestando muita atenção à precisão do percurso, à velocidade do fuso e às taxas de avanço.
b. Garantindo Precisão
- Medição e Inspeção: Depois de executar os programas de teste, meça as dimensões e o acabamento superficial das peças de teste usando instrumentos de medição de precisão. Compare os resultados com as especificações de projeto pretendidas.
- Inspeção de ferramentas: Inspecione as ferramentas de corte quanto a sinais de desgaste, como bordas lascadas ou desgaste excessivo da ferramenta. Substitua ou reafie as ferramentas conforme necessário.
- Inspeção da peça: Examine a peça de teste em busca de quaisquer defeitos, problemas de acabamento superficial ou desvios da geometria desejada. Resolva quaisquer problemas identificados durante a inspeção.
- Feedback e análise: Analise os resultados do teste para identificar quaisquer discrepâncias ou desvios dos resultados esperados. Determine se ajustes são necessários para melhorar a precisão.
c. Afinação
- Otimização de Percurso: Se os resultados dos testes revelarem imprecisões ou problemas de acabamento superficial, considere otimizar os percursos da ferramenta no seu software CAM. Ajuste os parâmetros do percurso, a seleção de ferramentas e as velocidades e avanços de corte conforme necessário.
- Ajustes de parâmetros da máquina: Consulte a documentação da máquina para ajustar parâmetros específicos, como aceleração, desaceleração e compensação de folga. Esses ajustes podem aumentar a precisão.
- Calibração de deslocamento da ferramenta: Recalibre os deslocamentos da ferramenta, se necessário. Garanta que a máquina compense com precisão o comprimento e o diâmetro da ferramenta, reduzindo erros na usinagem.
- Correção de deslocamento de trabalho: Verifique e corrija os deslocamentos de trabalho para garantir que a máquina posicione a ferramenta com precisão em relação à peça de trabalho. Pequenos erros no deslocamento de ponto zero podem levar a imprecisões significativas.
- Teste novamente: Depois de fazer ajustes e ajustes finos, execute novamente os programas de teste para verificar as melhorias na precisão e no acabamento superficial.
- Documentação: Documente todas as atividades de ajuste fino, ajustes e resultados de testes para referência futura. Esta documentação será valiosa para manter a consistência em suas operações de usinagem.
Capítulo 11: Treinamento e Desenvolvimento de Habilidades
Neste capítulo, enfatizaremos a importância do treinamento e do desenvolvimento de habilidades tanto para os operadores de máquinas quanto para o pessoal de manutenção. O treinamento adequado e o aprimoramento de habilidades são cruciais para garantir a operação segura e eficiente da máquina CNC, bem como para manter e solucionar problemas do equipamento de maneira eficaz.a. Treinamento de Operadores
- Operação básica da máquina: Os operadores devem receber treinamento abrangente sobre os aspectos fundamentais da operação de máquinas CNC, incluindo inicialização, desligamento, retorno à posição inicial e jogging da máquina.
- Compreendendo os códigos G e códigos M: Os operadores devem ser proficientes na interpretação e modificação de códigos G e códigos M, que controlam os movimentos e funções da máquina.
- Manuseio de ferramentas: Técnicas adequadas de manuseio de ferramentas, incluindo trocas de ferramentas, deslocamentos de ferramentas e calibração de ferramentas, são essenciais para evitar acidentes e garantir a precisão da usinagem.
- Configuração da peça de trabalho: O treinamento deve abranger a configuração da peça de trabalho, incluindo fixação da peça de trabalho, carregamento de material e fixação das peças de trabalho à mesa de trabalho ou acessório da máquina.
- Procedimentos de segurança: Os operadores devem ser bem versados nos procedimentos de segurança das máquinas CNC, protocolos de desligamento de emergência e uso de equipamentos de proteção individual (EPI).
- Noções básicas de solução de problemas: Habilidades básicas de solução de problemas, como identificar problemas comuns e saber quando procurar assistência, podem ajudar os operadores a resolver problemas menores rapidamente.
- Controle de Qualidade: O treinamento em controle de qualidade e técnicas de inspeção é vital para garantir que as peças acabadas atendam às tolerâncias especificadas e aos requisitos de acabamento superficial.
- Simulação e Prática: Os operadores devem ter oportunidades de prática prática e exercícios de simulação para aprimorar suas habilidades e aumentar a confiança na operação da máquina CNC.
b. Treinamento de manutenção
- Manutenção preventiva: O pessoal de manutenção deve receber treinamento nas tarefas rotineiras de manutenção preventiva específicas da máquina CNC, incluindo rotinas de lubrificação, limpeza e inspeção.
- Componentes da máquina: Um conhecimento profundo dos componentes da máquina, incluindo motores, sensores, acionamentos e sistemas elétricos, é necessário para que o pessoal de manutenção diagnostique e resolva problemas de forma eficaz.
- Técnicas de solução de problemas: Habilidades avançadas de solução de problemas, como diagnóstico de problemas elétricos, mecânicos e relacionados a software, são essenciais para minimizar o tempo de inatividade e otimizar o desempenho da máquina.
- Lubrificação e gerenciamento de fluidos: O conhecimento adequado dos pontos de lubrificação, tipos de fluidos e sistemas de filtragem é fundamental para manter a integridade mecânica da máquina.
- Sistemas elétricos: O pessoal de manutenção deve ser treinado em sistemas elétricos, incluindo a compreensão de diagramas de fiação, protocolos de segurança elétrica e substituição de componentes elétricos.
- Calibração Avançada: O treinamento em técnicas avançadas de calibração, como alinhamento a laser e medição de desvio do fuso, pode melhorar a precisão da máquina CNC.
- Atualizações de software: A familiaridade com atualizações de software e firmware é importante para manter o software de controle e o firmware da máquina atualizados.
c. Aprimoramento de habilidades
- Aprendizagem Contínua: Incentive uma cultura de aprendizagem contínua entre operadores e pessoal de manutenção. Isso pode incluir a participação em workshops, seminários e cursos on-line relacionados à tecnologia CNC.
- Avaliação de habilidades: Avalie periodicamente as habilidades e o conhecimento dos operadores e da equipe de manutenção para identificar áreas de melhoria e treinamento direcionado.
- Treinamento cruzado: Considere o treinamento cruzado de operadores em tarefas básicas de manutenção e vice-versa. Isso pode melhorar a compreensão geral e a colaboração dentro da equipe.
- Mentoria: Implemente programas de mentoria onde funcionários experientes possam orientar e compartilhar seus conhecimentos com membros da equipe menos experientes.
- Solução de problemas: Incentive os funcionários a se envolverem ativamente em exercícios de resolução de problemas e análise de causa raiz, promovendo uma cultura de solução de problemas proativa.
- Loop de feedback: Estabeleça um ciclo de feedback onde operadores e pessoal de manutenção possam comunicar problemas, compartilhar insights e sugerir melhorias para operação e manutenção de máquinas.
Conclusão
Neste guia completo, exploramos o intrincado processo de instalação de máquinas CNC, cobrindo uma ampla gama de tópicos para garantir que sua máquina CNC seja montada, instalada e operada de forma eficaz e segura. Vamos resumir os pontos principais, enfatizar a importância da instalação adequada da máquina CNC e olhar para o futuro da tecnologia CNC.a. Resumo dos pontos principais
Ao longo deste guia, cobrimos os seguintes pontos principais:- Compreendendo as máquinas CNC: Começamos discutindo o que são máquinas CNC, os vários tipos disponíveis e seus componentes essenciais.
- Preparação de pré-instalação: Enfatizamos a importância de preparar o espaço de trabalho, atender aos requisitos de energia e elétricos e implementar medidas de segurança antes da instalação.
- Montagem da Máquina CNC: Foram fornecidas etapas detalhadas para desembalar, organizar componentes, montar a estrutura da máquina, conectar motores e acionamentos, instalar o painel de controle e gerenciar cabos.
- Alinhamento e Nivelamento: Discutimos a importância do alinhamento e nivelamento, as ferramentas necessárias e o processo passo a passo para obter um alinhamento preciso.
- Fiação elétrica: Compreender os sistemas elétricos, conectar a máquina CNC e seguir as precauções de segurança durante o trabalho elétrico foram abordados detalhadamente.
- Instalando o software de controle: A instalação do software de controle, calibração e procedimentos de teste foram discutidos para garantir que a máquina CNC funcione corretamente.
- Lubrificação e Manutenção: Foi destacada a importância da lubrificação e manutenção para a longevidade e desempenho da máquina, incluindo pontos de lubrificação e cronogramas de manutenção.
- Procedimentos de segurança: Procedimentos de segurança, protocolos de desligamento de emergência e uso de equipamentos de proteção individual (EPI) foram abordados para criar um ambiente de trabalho seguro.
- Solução de problemas comuns de instalação: Problemas comuns e técnicas de solução de problemas foram fornecidos para ajudar a identificar e resolver problemas de forma eficaz.
- Verificações e testes finais: A execução de programas de teste, a garantia da precisão e o ajuste fino da máquina foram discutidos para alcançar o desempenho ideal.
- Treinamento e Desenvolvimento de Habilidades: A importância do treinamento do pessoal de operação e manutenção, bem como do aprimoramento contínuo de habilidades, foi enfatizada.
b. A importância da instalação adequada da máquina CNC
A instalação adequada da máquina CNC é a base sobre a qual é construída uma operação de usinagem bem-sucedida. É essencial pelos seguintes motivos:- Precisão: Uma máquina CNC bem instalada tem maior probabilidade de produzir peças precisas e precisas, reduzindo desperdícios e retrabalhos.
- Segurança: A instalação que segue os padrões e procedimentos de segurança garante o bem-estar dos operadores da máquina e do pessoal de manutenção.
- Longevidade: A instalação correta e a manutenção regular prolongam a vida útil da sua máquina CNC, protegendo o seu investimento.
- Eficiência: Uma máquina instalada corretamente opera com eficiência, minimizando o tempo de inatividade e maximizando a produtividade.
- Qualidade: A qualidade da instalação afeta diretamente a qualidade das peças usinadas, levando a clientes satisfeitos e melhorando a reputação.
c. Olhando para o futuro
À medida que a tecnologia continua a avançar, as máquinas CNC tornar-se-ão ainda mais capazes e versáteis. É essencial manter-se informado sobre os últimos desenvolvimentos, atualizações de software e melhores práticas em usinagem CNC. Além disso, à medida que a tecnologia CNC se torna mais acessível, mais indústrias e empresas podem beneficiar das suas vantagens. Concluindo, a instalação de máquinas CNC é um processo complexo, mas gratificante. Seguindo as diretrizes e práticas recomendadas descritas neste guia, você pode preparar o terreno para uma operação de usinagem CNC bem-sucedida. Lembre-se de que o aprendizado contínuo, o treinamento e a manutenção contínua são essenciais para manter e melhorar o desempenho de suas máquinas CNC enquanto você olha para um futuro repleto de oportunidades no mundo da fabricação de precisão.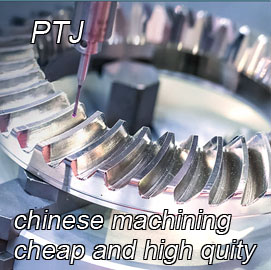
Serviços
- 5 eixos de usinagem
- Fresagem CNC
- Torneamento CNC
- Indústrias de usinagem
- Processo de usinagem
- Tratamento da superfície
- Usinagem de Metal
- Usinagem de Plástico
- Molde de metalurgia do pó
- Fundição
- Galeria de peças
Estudos de Caso
- Peças de metal automotivo
- Peças de máquinas
- Dissipador de calor LED
- Peças de Construção
- Peças Móveis
- Peças Médicas
- Partes eletrônicas
- Usinagem Sob Medida
- Peças de bicicleta
Lista de materiais
- Usinagem de Alumínio
- Usinagem de titânio
- Usinagem de aço inoxidável
- Usinagem de cobre
- Usinagem de latão
- Usinagem de Super Liga
- Peek Usinagem
- Usinagem UHMW
- Usinagem Unilate
- PA6 Usinagem
- Usinagem PPS
- Usinagem de Teflon
- Usinagem Inconel
- Usinagem de aço ferramenta
- Mais material
Galeria de peças