Um guia completo sobre como configurar uma ferramenta de corte de torno
Configurar uma ferramenta de corte de torno é uma habilidade fundamental para qualquer maquinista, especialmente quando se trata de tornos com controle numérico computadorizado (CNC). O ajuste adequado da ferramenta é crucial para obter resultados de usinagem precisos e precisos. Neste guia completo, nos aprofundaremos nos detalhes intrincados de como configurar uma ferramenta de corte de torno para torneamento CNC. Desde os conceitos básicos dos componentes da ferramenta de torno até técnicas avançadas para otimizar o desempenho de corte, este artigo tem como objetivo fornecer uma compreensão abrangente do processo. Ao final deste guia, você terá o conhecimento e as habilidades necessárias para configurar uma ferramenta de torno com confiança e precisão, garantindo ótimos resultados em suas operações de torneamento CNC.
Compreendendo as ferramentas de corte do torno
No mundo da usinagem, as ferramentas de corte do torno são componentes indispensáveis para moldar e transformar matérias-primas em peças de engenharia de precisão. Esteja você trabalhando com tornos manuais tradicionais ou tornos CNC avançados, é essencial ter um conhecimento profundo das ferramentas de corte do torno. Nesta seção, nos aprofundaremos nas características, funções e tipos de ferramentas de corte de torno.
Características das ferramentas de corte de torno
As ferramentas de corte de torno são projetadas para realizar uma variedade de operações de usinagem, como torneamento, faceamento, canal, rosqueamento e muito mais. Essas ferramentas compartilham várias características comuns:
- Dureza: As ferramentas de corte de torno são normalmente feitas de aço rápido (HSS), metal duro ou outros materiais de ferramentas especializados. Esses materiais são escolhidos pela sua dureza, permitindo que a ferramenta resista às altas temperaturas e pressões geradas durante o corte.
- Ponta: A aresta de corte de uma ferramenta de torno é a parte que realmente remove o material da peça de trabalho. Ela foi projetada para ser nítida e precisa, e a geometria da aresta de corte pode variar dependendo da tarefa específica à qual a ferramenta se destina.
- Shank: A haste da ferramenta de torno é a peça fixada no porta-ferramenta. Proporciona estabilidade e rigidez à ferramenta durante o Processo de usinagem. Os designs das hastes podem diferir com base no tipo de ferramenta e nas especificações do fabricante.
- Suporte de ferramenta: O porta-ferramenta é um componente crucial, especialmente no torneamento CNC, pois mantém a ferramenta do torno no lugar com segurança. Deve fornecer estabilidade, precisão e facilidade de ajuste para garantir o desempenho ideal da ferramenta.
- geometria: A geometria da ferramenta de corte, incluindo o ângulo de saída, o ângulo de folga e o quebra-cavacos, desempenha um papel significativo na determinação do desempenho da ferramenta. A geometria adequada é essencial para obter remoção eficiente de material e evacuação de cavacos.
- Revestimento: Muitas ferramentas de corte de torno vêm com revestimentos especializados, como TiN (nitreto de titânio) ou TiAlN (nitreto de alumínio e titânio), para aumentar a vida útil da ferramenta, reduzir o atrito e melhorar o desempenho.
Funções das ferramentas de corte de torno
As ferramentas de corte do torno desempenham diversas funções fundamentais no processo de usinagem:
- Remoção de Materiais: A principal função das ferramentas de corte do torno é remover material de uma peça de trabalho. Essa remoção pode ocorrer por meio de torneamento (girando a peça durante o corte), faceamento (criação de uma superfície plana) ou outras operações.
- Controle Dimensional: As ferramentas de corte são responsáveis por garantir que as dimensões da peça usinada correspondam às especificações desejadas. O controle preciso é essencial para alcançar resultados precisos e consistentes.
- Acabamento de superfície: A qualidade do acabamento superficial é determinada pela nitidez da ferramenta de corte, geometria e parâmetros de corte utilizados. Uma ferramenta de corte bem conservada e configurada corretamente contribui para um acabamento superficial liso e fino.
- Controle de Chip: O controle eficaz de cavacos é essencial para evitar o acúmulo de cavacos e manter um ambiente de trabalho limpo e seguro. O quebra-cavacos em algumas ferramentas ajuda a facilitar a remoção de cavacos.
- Eficiência: As ferramentas de corte de torno são projetadas para tornar os processos de usinagem eficientes e econômicos. Eles ajudam a minimizar o desperdício de material e a otimizar a vida útil da ferramenta, reduzindo os custos de produção.
Tipos de ferramentas de corte de torno
As ferramentas de corte de torno estão disponíveis em vários tipos, cada um adaptado para tarefas específicas de usinagem. Aqui estão alguns tipos comuns:
- Ferramentas de torneamento: Essas ferramentas são versáteis e utilizadas para operações de torneamento cilíndrico. Eles podem moldar as superfícies externas e internas de uma peça.
- Ferramentas chatas: Ferramentas de mandrilamento são empregadas para ampliar ou finalizar furos existentes. Eles são projetados para precisão e exatidão na usinagem de furos.
- Ferramentas de partição: Ferramentas de corte são usadas para separar uma peça de um material maior. Eles criam linhas de partição definidas com desperdício mínimo.
- Ferramentas de rosqueamento: As ferramentas de rosqueamento são usadas para cortar roscas em uma peça de trabalho. Eles vêm em vários formatos e tamanhos para diferentes requisitos de rosqueamento.
- Ferramentas de canal: As ferramentas de canal criam ranhuras ou reentrâncias em uma peça de trabalho, normalmente para acomodar anéis de vedação, anéis de retenção ou outros recursos.
- Ferramentas de enfrentamento: As ferramentas de faceamento são projetadas para criar superfícies planas na extremidade de uma peça de trabalho. Eles são frequentemente usados para obter superfícies perpendiculares ou remover material da extremidade de uma peça de trabalho.
Compreender as características e funções das ferramentas de corte do torno é essencial para selecionar a ferramenta certa para uma tarefa de usinagem específica. A escolha da ferramenta de corte pode impactar significativamente a qualidade e a eficiência do processo de usinagem, tornando-se uma decisão crítica em qualquer operação de torno. Além disso, a manutenção adequada e a configuração da ferramenta são vitais para garantir resultados consistentes e precisos, que serão discutidos em mais detalhes posteriormente neste guia.
Tipos de ferramentas de corte de torno
As ferramentas de corte de torno vêm em vários tipos, cada uma projetada especificamente para uma tarefa específica de usinagem. Compreender esses diferentes tipos de ferramentas de corte e suas aplicações é essencial para selecionar a ferramenta certa para um determinado trabalho. Aqui estão alguns tipos comuns de ferramentas de corte de torno:
Ferramentas de torneamento:
- Ferramenta de ponta redonda: Usado para operações de torneamento de uso geral. Possui aresta de corte arredondada e é adequada tanto para cortes de desbaste quanto de acabamento.
- Ferramenta de diamante: Nomeada por sua aresta de corte em formato de diamante, é ideal para usinagem precisa em diversos materiais, incluindo metais e plásticos.
- Ferramenta de nariz quadrado: Apresenta uma aresta de corte quadrada e normalmente é usada para operações de faceamento e torneamento de cantos a XNUMX graus.
Ferramentas chatas:Barra chata interna: Usado para ampliar e finalizar furos existentes em uma peça de trabalho. Ele é projetado para precisão e pode criar dimensões internas precisas.
Ferramentas de partição:Lâmina de separação: Essas ferramentas são usadas para cortar uma peça de um material maior. Eles criam uma linha de partição definida com desperdício mínimo.
Ferramentas de rosqueamento:
- Ferramenta de corte de linha: Projetado para criar roscas externas em uma peça de trabalho. Eles vêm em vários formatos e tamanhos para diferentes requisitos de rosqueamento.
- Ferramenta de perseguição de linha: Usado para perseguir ou restaurar threads existentes. Essas ferramentas são comumente usadas para reparo de roscas.
Ferramentas de canal:Ferramenta de Ranhura: Essas ferramentas criam ranhuras ou reentrâncias em uma peça de trabalho, geralmente para acomodar anéis de vedação, anéis de retenção ou outros recursos.
Ferramentas de enfrentamento:Ferramenta de enfrentamento: Usado para criar superfícies planas na extremidade de uma peça de trabalho. É frequentemente usado para obter superfícies perpendiculares ou remover material da extremidade de uma peça de trabalho.
Ferramentas para cortes e canais:Ferramenta de combinação: Essas ferramentas versáteis são projetadas para operações de corte e canal, economizando tempo e trocas de ferramentas.
Ferramentas para rosqueamento e canal:Ferramenta combinada para rosqueamento e canal: Ideal para trabalhos que exigem operações de rosqueamento e canal na mesma peça.
Ferramentas de chanfrar:Ferramenta de chanfrar: Usado para criar chanfros ou bordas chanfradas na peça de trabalho. Chanfros são frequentemente aplicados para melhorar a aparência e facilitar a montagem de peças usinadas.
Ferramentas serrilhadas:Ferramenta serrilhada: Serrilhado é um processo de criação de um padrão texturizado em uma peça de trabalho, normalmente para melhorar a aderência ou a estética. As ferramentas recartilhadas vêm em vários padrões e designs.
Ferramentas de modelagem:Ferramenta de formulário: Essas ferramentas são projetadas de forma personalizada para geometrias específicas de peças, frequentemente usadas para produzir formas complexas e não padronizadas.
Ferramentas especiais:Ferramentas de perfil: Usado para criar perfis complexos em uma peça.
Ferramentas de enfrentamento e torneamento: Eles são projetados para operações de faceamento e torneamento.
Ferramentas de corte: Projetado para cortar a peça de trabalho para criar peças separadas ou remover o excesso de material.
A seleção da ferramenta de corte correta depende de fatores como o material a ser usinado, o acabamento desejado, as dimensões exigidas e a operação específica que está sendo executada. É essencial escolher a ferramenta adequada e mantê-la adequadamente para garantir uma usinagem eficiente e precisa. A seleção adequada da ferramenta, juntamente com a configuração e o ajuste corretos, são cruciais para obter resultados de alta qualidade em operações de torno.
Componentes de uma ferramenta de corte de torno
Uma ferramenta de corte de torno é um instrumento de precisão projetado para moldar, cortar e remover material de uma peça de trabalho. Para entender como funciona e como configurá-lo corretamente, é fundamental estar familiarizado com seus diversos componentes. Aqui estão os principais componentes de uma ferramenta de corte de torno:
- Suporte de ferramenta:O porta-ferramenta é a peça que fixa a ferramenta de corte no lugar. Ele se fixa ao porta-ferramentas do torno e fornece a rigidez e estabilidade necessárias para as operações de usinagem. Os porta-ferramentas vêm em vários designs para acomodar diferentes tipos de ferramentas de corte.
- Shank:A haste é a parte da ferramenta de corte que cabe no porta-ferramenta. Geralmente é cilíndrico e está preso com segurança dentro do suporte. As dimensões e o formato da haste podem variar de acordo com o tipo e design da ferramenta.
- Ponta:A aresta de corte é a parte afiada da ferramenta que entra em contato e remove material da peça de trabalho. A qualidade da aresta de corte e sua geometria afetam significativamente o desempenho de corte e o acabamento superficial. É essencial manter a nitidez e a precisão da ponta.
- Inserção:Muitas ferramentas de corte modernas usam pastilhas substituíveis, que normalmente são feitas de materiais duros como metal duro ou cerâmica. Essas pastilhas possuem a geometria de corte e são fixadas em um bolsão na ferramenta de corte. Eles podem ser girados ou substituídos quando estiverem desgastados ou danificados, prolongando a vida útil da ferramenta.
- Nariz da ferramenta:A ponta da ferramenta é a ponta da ferramenta de corte onde a aresta de corte e a pastilha (se usada) se unem. A ponta da ferramenta deve ser posicionada e alinhada com precisão para uma usinagem precisa. Algumas ferramentas de corte de torno possuem um raio de ponta ajustável para melhor controle sobre o desempenho da ferramenta.
- Flanco da ferramenta:O flanco da ferramenta é a superfície lateral da ferramenta de corte que não faz parte da aresta de corte. Ângulos de folga adequados no flanco da ferramenta garantem o escoamento dos cavacos e reduzem o atrito entre a ferramenta e a peça de trabalho.
- Face do ancinho da ferramenta:A face de saída é a superfície da ferramenta de corte voltada para a peça de trabalho. O ângulo e a condição da face de saída afetam a formação de cavacos e a eficiência do processo de corte. O ângulo de inclinação é um aspecto crítico da geometria da ferramenta.
- Ângulo de alívio da ferramenta:O ângulo de relevo é o ângulo entre o flanco da ferramenta e o eixo da ferramenta. Garante que a aresta de corte não esfregue na peça de trabalho, reduzindo o atrito e a geração de calor.
- Ângulo de folga da ferramenta:O ângulo de incidência é o ângulo entre a face de saída e a superfície da peça. Permite que os cavacos fluam suavemente e evita interferência entre a ferramenta e a peça de trabalho.
- Quebra-cavacos (se aplicável):Algumas ferramentas de corte, especialmente aquelas utilizadas para operações de desbaste, apresentam um quebra-cavacos, uma ranhura ou entalhe na face de saída. O quebra-cavacos ajuda a controlar a formação de cavacos e melhorar o escoamento de cavacos.
A montagem, o alinhamento e a manutenção adequados desses componentes são essenciais para obter uma usinagem precisa e eficiente. A escolha da ferramenta de corte e sua configuração devem ser adaptadas à operação de usinagem específica e ao material a ser trabalhado. A inspeção e manutenção regulares dos componentes da ferramenta de corte também são necessárias para garantir resultados consistentes e de alta qualidade.
Escolhendo a ferramenta de corte certa para o trabalho
Selecionar a ferramenta de corte correta é uma decisão crítica em qualquer operação de usinagem, pois influencia muito a qualidade, eficiência e precisão do trabalho. Vários fatores devem ser considerados ao escolher a ferramenta de corte apropriada para um trabalho específico. Aqui está um guia sobre como escolher a ferramenta de corte certa para o seu projeto de usinagem:
1. Material da peça:
O material que você está usinando é um dos fatores mais críticos na seleção da ferramenta. Diferentes materiais têm dureza, condutividade térmica e abrasividade variadas. Considere o seguinte:
- Dureza: Materiais duros como aço temperado ou cerâmica requerem ferramentas de corte com arestas de corte duras, como pastilhas de metal duro, para suportar as altas forças de corte.
- Materiais macios: Para materiais mais macios, como alumínio ou plástico, aço rápido (HSS) ou outros materiais de ferramenta podem ser suficientes.
2. Operação de usinagem:
A operação específica que você está executando, como torneamento, fresamento, furação, rosqueamento ou canal, determinará o tipo de ferramenta de corte necessária. Diferentes ferramentas são projetadas para diversas tarefas, e a escolha da ferramenta certa garante um desempenho ideal.
3. Velocidade de corte e taxa de avanço:
Determine a velocidade de corte e a taxa de avanço necessárias com base no material e na operação de usinagem. Os fabricantes de ferramentas de corte fornecem recomendações para esses parâmetros com base no design da ferramenta e no material que está sendo usinado. Seguir essas recomendações é crucial para alcançar os resultados desejados.
4. Geometria da Ferramenta:
Considere a geometria da ferramenta de corte, incluindo o ângulo de saída, o ângulo de folga e o raio da ponta da ferramenta. A geometria da ferramenta deve corresponder ao material e ao tipo de corte. Por exemplo, um ângulo de inclinação positivo é adequado para materiais mais macios, enquanto um ângulo de inclinação negativo é melhor para materiais mais duros.
5. Dimensões da peça:
O tamanho e as dimensões da peça também influenciam a seleção da ferramenta. Algumas ferramentas de corte são mais adequadas para operações de desbaste para remover rapidamente material a granel, enquanto outras são projetadas para acabamento para obter dimensões e acabamentos superficiais precisos.
6. Requisitos de acabamento de superfície:
Se você precisar de um acabamento superficial específico, selecione uma ferramenta de corte com geometria e nitidez apropriadas. As ferramentas de acabamento são projetadas para fornecer um acabamento superficial mais liso, enquanto as ferramentas de desbaste são mais eficientes para remoção de material.
7. Material da ferramenta:
A escolha do material da ferramenta é crucial. Ferramentas de metal duro, aço rápido (HSS), cerâmica e revestidas têm suas vantagens e limitações. Considere fatores como vida útil da ferramenta, resistência ao desgaste e custo do material da ferramenta em sua decisão.
8. Líquido refrigerante e lubrificação:
Considere se a operação de corte requer refrigeração ou lubrificação. Alguns materiais geram calor excessivo durante a usinagem e o uso do líquido refrigerante ou lubrificante correto pode prolongar a vida útil da ferramenta e melhorar o desempenho de corte.
9. Revestimentos de ferramentas:
Muitas ferramentas de corte modernas vêm com revestimentos especializados como TiN (nitreto de titânio) ou TiAlN (nitreto de alumínio e titânio) para melhorar a resistência ao desgaste e reduzir o atrito. Escolha uma ferramenta com revestimento apropriado para sua aplicação específica.
10. Considerações de custo:
Equilibrar o custo da ferramenta de corte com o seu desempenho e longevidade é crucial. Embora as ferramentas premium possam oferecer maior vida útil e melhor desempenho, é essencial encontrar um equilíbrio que se alinhe ao orçamento do seu projeto.
11. Compatibilidade do porta-ferramentas e da máquina:
Certifique-se de que a ferramenta de corte escolhida seja compatível com o sistema porta-ferramentas do seu torno ou centro de usinagem. O porta-ferramenta deve proporcionar estabilidade e rigidez à ferramenta de corte durante o processo de usinagem.
Em última análise, a ferramenta de corte certa para o trabalho dependerá de uma combinação destes factores. Sempre consulte as recomendações do fabricante da ferramenta e considere procurar aconselhamento de maquinistas experientes ou especialistas em ferramentas se não tiver certeza. A seleção e configuração adequadas da ferramenta são fundamentais para obter resultados de usinagem eficientes e precisos.
Configurando a ferramenta de corte do torno
Configurar uma ferramenta de torno para torneamento CNC é um processo sistemático que envolve várias etapas cruciais. Cada etapa é vital para garantir que a ferramenta de corte esteja corretamente posicionada e alinhada, resultando em uma usinagem precisa e eficiente. Vamos percorrer o processo passo a passo:
Passo 1: Preparando o Torno e a Peça de Trabalho
Antes de configurar a ferramenta de corte, é essencial preparar o torno e a peça:
- Prenda a peça de trabalho: Certifique-se de que a peça de trabalho esteja firmemente fixada no mandril ou pinça do torno. Certifique-se de que ele gira suavemente, sem qualquer oscilação ou vibração.
- Segurança: Certifique-se de que todas as medidas de segurança estejam em vigor, incluindo o uso de equipamento de proteção individual (EPI) adequado e as configurações corretas do torno.
Etapa 2: Selecionando o porta-ferramentas correto
O porta-ferramentas é um componente crítico no processo de configuração. Escolha o porta-ferramenta apropriado com base em fatores como o tipo de ferramenta de corte, a operação que está sendo executada e o sistema de porta-ferramentas do torno.
- Combine o suporte da ferramenta com a ferramenta de corte: Certifique-se de que o porta-ferramenta seja compatível com o tipo e tamanho da ferramenta de corte que você pretende usar.
- Rigidez do porta-ferramentas: Escolha um porta-ferramentas que proporcione estabilidade e rigidez. Isto é especialmente importante em aplicações de alta precisão.
Passo 3: Montagem da Ferramenta de Corte
A montagem da ferramenta de corte envolve fixá-la no porta-ferramentas e garantir que esteja firme e corretamente posicionada:
- Prenda a ferramenta de corte: Insira a ferramenta de corte no suporte da ferramenta e aperte todos os mecanismos de fixação, como parafusos de fixação ou pinças. Certifique-se de que a ferramenta seja segurada com segurança.
- Orientação: Verifique se a ferramenta de corte está orientada corretamente em relação à peça de trabalho. A ferramenta deve ser posicionada para engatar a peça de trabalho no ângulo e profundidade desejados.
Etapa 4: Ajustar a altura da ferramenta e o alinhamento da linha central
A altura correta da ferramenta e o alinhamento da linha central são cruciais para obter dimensões de usinagem precisas:
- Ajuste de altura da ferramenta: Ajuste a altura da ferramenta para alinhá-la com a linha central do fuso do torno. Use um medidor de altura da ferramenta ou uma barra de teste para definir a ferramenta na altura correta.
- Alinhamento da linha central: Certifique-se de que a ferramenta esteja alinhada com a linha central do fuso do torno. O desalinhamento pode resultar em usinagem descentralizada, afetando a precisão da peça.
Etapa 5: Definir a compensação do raio da ponta da ferramenta
Para torneamento CNC, a compensação do raio da ponta da ferramenta leva em conta a geometria da ferramenta de corte. Isto é particularmente importante ao usar ferramentas de inserção:
- Determine o raio da ponta da ferramenta: Meça ou procure o raio exato da ponta da pastilha da ferramenta de corte que você está usando.
- Insira o valor do raio: No software de controle CNC, insira o valor medido do raio da ponta da ferramenta para garantir que a máquina compense a geometria da ferramenta durante a usinagem.
Etapa 6: Definir deslocamentos de ferramenta
Os deslocamentos da ferramenta levam em conta variações nas dimensões da ferramenta e na geometria da peça. Eles garantem que a posição da ferramenta seja ajustada com precisão para usinagem:
- Selecione o deslocamento correto da ferramenta: Determine o valor de correção da ferramenta apropriado com base na geometria da ferramenta e na operação de usinagem. Este valor de deslocamento compensa quaisquer discrepâncias.
- Insira os valores de deslocamento: Insira os valores de deslocamento escolhidos no software de controle CNC. Esses valores instruirão a máquina sobre como ajustar a posição da ferramenta com precisão.
Durante todo o processo de configuração da ferramenta, use instrumentos de medição de precisão, como micrômetros, medidores de altura e comparadores para verificar e ajustar o alinhamento da ferramenta. Inspecione e mantenha regularmente a ferramenta de corte para garantir que ela permaneça afiada e em boas condições, pois uma ferramenta bem conservada contribui para resultados de usinagem consistentes e precisos.
A configuração adequada da ferramenta de corte do torno nessas etapas é crucial para obter resultados ideais nas operações de torneamento CNC. Precisão e atenção aos detalhes durante a configuração da ferramenta são fatores-chave na produção de peças usinadas de alta qualidade.
Otimizando Parâmetros de Corte para Torneamento CNC
A otimização dos parâmetros de corte é essencial para obter operações de torneamento CNC eficientes e de alta qualidade. Os quatro aspectos principais a serem considerados ao otimizar os parâmetros de corte são velocidades e avanços, profundidade de corte, fluidos e lubrificantes de corte e gerenciamento da vida útil da ferramenta.
1. Velocidades e avanços:
- a. Velocidade de corte (velocidade superficial):A velocidade de corte, muitas vezes referida como velocidade superficial, é a velocidade na qual a peça de trabalho e a ferramenta de corte interagem. É medido em pés superficiais por minuto (SFM) ou metros por minuto (m/min). Para otimizar a velocidade de corte, considere o material que está sendo usinado e o material da ferramenta. Ferramentas de aço rápido (HSS) têm velocidades de corte recomendadas mais baixas do que ferramentas de metal duro, por exemplo. Consulte os dados do fabricante da ferramenta ou manuais de usinagem para determinar as velocidades de corte recomendadas para materiais e ferramentas específicas.
- b. Taxa de alimentação:A taxa de avanço é a velocidade linear na qual a ferramenta de corte avança na peça de trabalho. É medido em polegadas por revolução (IPR) ou milímetros por revolução (mm/rev). Para otimizar a taxa de avanço, considere fatores como propriedades do material, geometria da ferramenta e o acabamento superficial desejado. Taxas de avanço mais altas geralmente são mais produtivas, mas podem exigir ferramentas mais robustas.
- c. Relação entre velocidade de corte e taxa de avanço:Equilibrar a velocidade de corte e a taxa de avanço é crucial para uma remoção eficiente de material. Um aumento na velocidade de corte normalmente permite uma taxa de avanço mais alta, mas os dois devem ser ajustados juntos para evitar desgaste e superaquecimento da ferramenta.
2. Profundidade de corte:
- a. Profundidade de Corte (DOC):A profundidade de corte é a distância que a ferramenta de corte penetra na peça de trabalho. É essencial considerar as capacidades do material e da ferramenta. Otimize a profundidade de corte com base na dureza do material e na resistência e rigidez da ferramenta. Cortes superficiais podem ser necessários para materiais mais duros, enquanto cortes mais profundos podem ser obtidos em materiais mais macios.
- b. Profundidade de corte axial e radial:No torneamento CNC, considere a profundidade de corte axial (ao longo do comprimento da peça) e radial (ao longo do diâmetro da peça). As profundidades ideais para cada um variam de acordo com a operação e o material.
3. Fluidos de corte e lubrificantes:
- a. Selecionando o fluido de corte correto:Os fluidos de corte são essenciais para dissipar o calor, reduzir o atrito e melhorar o escoamento dos cavacos. Escolha o fluido de corte apropriado com base no material e na operação de usinagem. Refrigerantes solúveis em água, à base de óleo mineral ou sintéticos podem ser preferidos para diferentes materiais.
- b. Aplicação adequada:Aplique fluidos de corte de forma eficaz na área de corte para garantir lubrificação e resfriamento adequados. Isso pode ser feito por meio de resfriamento por inundação, sistemas de névoa ou fornecimento de líquido refrigerante através da ferramenta, dependendo das capacidades da máquina.
- c. Monitoramento e Manutenção:Monitore regularmente os níveis, condições e contaminação do fluido de corte para garantir que permaneçam eficazes. Mantenha os sistemas de fluidos de corte para evitar problemas como crescimento e degradação bacteriana.
4. Gerenciamento da vida útil da ferramenta:
- a. Inspeção e manutenção de ferramentas:Implemente um programa de rotina de inspeção e manutenção de ferramentas para garantir que as ferramentas estejam em boas condições. Ferramentas cegas ou danificadas podem resultar em má qualidade de usinagem e redução da vida útil da ferramenta.
- b. Cronograma de substituição de ferramentas:Estabeleça um cronograma de substituição de ferramentas com base em fatores como desgaste da ferramenta, tempo de atividade da máquina e requisitos de produção. Isso ajuda a evitar falhas inesperadas da ferramenta e a manter uma qualidade de usinagem consistente.
- c. Otimização da vida útil da ferramenta:Alguns materiais e revestimentos de ferramentas oferecem maior vida útil da ferramenta. Considere o uso de ferramentas de alto desempenho para otimizar a vida útil da ferramenta e reduzir o tempo de inatividade da produção.
- d. Controle de cavacos de ferramenta:O controle eficaz de cavacos, incluindo o uso de quebra-cavacos e geometria adequada da ferramenta, pode prolongar a vida útil da ferramenta, reduzindo o desgaste induzido por cavacos.
A otimização dos parâmetros de corte no torneamento CNC é um processo contínuo. Experimentação e ajuste fino podem ser necessários para encontrar os melhores parâmetros para uma aplicação específica. Monitore e ajuste regularmente esses parâmetros para garantir desempenho ideal de usinagem, vida útil da ferramenta e qualidade da peça. Parâmetros de corte adequadamente otimizados não apenas melhoram a eficiência da usinagem, mas também reduzem o desgaste da ferramenta e, em última análise, os custos de produção.
Solução de problemas comuns na configuração de ferramentas
A solução de problemas comuns na configuração de ferramentas é uma habilidade essencial para maquinistas e operadores CNC. Compreender e resolver esses problemas pode ajudar a manter a precisão e a qualidade das operações de usinagem. Aqui estão alguns problemas comuns de configuração de ferramentas e suas soluções:
1. Conversa de ferramenta:
Questão: A vibração da ferramenta ocorre quando a ferramenta de corte vibra durante o processo de usinagem, causando mau acabamento superficial, desgaste da ferramenta e possíveis danos à peça de trabalho.
Alternativa?
- Reduza a velocidade ou aumente o avanço: Ajuste os parâmetros de corte diminuindo a velocidade de corte ou aumentando a taxa de avanço. Essa mudança pode amortecer as vibrações e reduzir a vibração.
- Verifique a rigidez da ferramenta: Certifique-se de que o suporte da ferramenta e a ferramenta estão corretamente fixados e que a ferramenta não se estende muito do suporte.
- Verifique a fixação da peça: Certifique-se de que a peça de trabalho esteja fixada com segurança para evitar vibrações relacionadas à peça de trabalho.
- Use técnicas de amortecimento: Algumas máquinas vêm com recursos para amortecer vibrações. Se disponíveis, considere usá-los.
- Escolha uma ferramenta mais rígida: Uma ferramenta mais rígida, como uma com menos canais, pode ajudar a reduzir a vibração.
2. Mau acabamento superficial:
Questão: Um acabamento superficial ruim pode resultar de problemas com a configuração da ferramenta ou parâmetros de corte, levando a superfícies ásperas ou inconsistentes na peça de trabalho.
Alternativa?
- Verifique a geometria da ferramenta: Certifique-se de que a geometria da ferramenta de corte seja apropriada para a operação. Uma ferramenta afiada com a geometria correta é crucial para obter um bom acabamento superficial.
- Otimize os parâmetros de corte: Ajuste a velocidade de corte, o avanço e a profundidade de corte para encontrar a melhor combinação para o material e a operação específicos.
- Verifique se há desgaste da ferramenta: Inspecione a ferramenta quanto a sinais de desgaste ou danos, como bordas lascadas. Substitua ou reafie a ferramenta conforme necessário.
- Use fluido de corte apropriado: A lubrificação e o resfriamento adequados podem afetar significativamente o acabamento da superfície. Use o fluido de corte correto para o material e a operação.
- Minimizar a vibração: Resolva problemas de vibração para evitar a criação de irregularidades na superfície.
3. Imprecisões dimensionais:
Questão: As peças podem ter dimensões incorretas devido a ferramentas desalinhadas ou desgaste da ferramenta.
Alternativa?
- Verifique a configuração da ferramenta: Verifique se a ferramenta está corretamente configurada com a altura e alinhamento corretos em relação à peça de trabalho.
- Calibrar máquina: Certifique-se de que a máquina CNC esteja devidamente calibrada e que interprete com precisão os deslocamentos e os dados da ferramenta.
- Ajustar deslocamentos da ferramenta: Corrija quaisquer erros nos deslocamentos da ferramenta medindo a ferramenta com precisão e inserindo os valores de deslocamento adequados no controle CNC.
- Inspecione o desgaste da ferramenta: Inspecione regularmente a ferramenta de corte quanto a desgaste e substitua-a ou reafie-a quando necessário.
4. Problemas de controle de chips:
Questão: O controle inadequado de cavacos pode levar a problemas como entupimento de cavacos, evacuação inadequada de cavacos e danos à peça ou ferramenta.
Alternativa?
- Escolha a geometria correta da ferramenta: Selecione uma ferramenta de corte com quebra-cavacos ou geometria apropriada para o material e operação.
- Otimize os parâmetros de corte: Ajuste as taxas de avanço, velocidades de corte e profundidades de corte para otimizar a formação e evacuação de cavacos.
- Use lubrificação adequada: O uso adequado de fluidos de corte pode ajudar a lubrificar e facilitar o escoamento dos cavacos.
- Verifique o alinhamento da ferramenta e da peça: Certifique-se de que a ferramenta esteja corretamente alinhada com a peça de trabalho para evitar problemas relacionados a lascas.
5. Quebra de ferramenta:
Questão: A quebra da ferramenta pode ocorrer devido a força excessiva, configuração incorreta da ferramenta ou problemas relacionados ao material.
Alternativa?
- Otimize os parâmetros de corte: Reduza as forças de corte ajustando parâmetros como taxas de avanço, velocidades de corte e profundidades de corte.
- Verifique a configuração da ferramenta: Certifique-se de que a ferramenta esteja montada com segurança no porta-ferramentas e corretamente alinhada.
- Use material de ferramenta adequado: Escolha o material da ferramenta certo para o material específico que você está usinando. Por exemplo, ferramentas de metal duro são melhores para materiais duros.
- Inspecione quanto a desgaste da ferramenta: Verifique regularmente a ferramenta quanto a sinais de desgaste e substitua-a antes que fique excessivamente desgastada e propensa a quebrar.
Abordar esses problemas comuns de configuração de ferramentas requer uma combinação de treinamento adequado, manutenção regular e uma abordagem sistemática para solução de problemas. A capacidade de diagnosticar e resolver problemas relacionados a ferramentas é fundamental para obter resultados de usinagem eficientes e de alta qualidade.
Conclusão
O processo de configuração e otimização de ferramentas de torno para torneamento CNC é um aspecto crucial da usinagem que impacta significativamente a qualidade, eficiência e precisão dos processos de fabricação. Um profundo conhecimento dos componentes e funções das ferramentas de corte, bem como dos fatores envolvidos na seleção das ferramentas, é essencial para maquinistas e operadores CNC.
A configuração adequada de uma ferramenta de corte envolve uma abordagem sistemática, desde a preparação do torno e da peça de trabalho até a seleção do porta-ferramenta correto, montagem da ferramenta, ajuste da altura da ferramenta e alinhamento da linha central e configuração da compensação do raio da ponta da ferramenta e dos deslocamentos da ferramenta. Cada etapa desempenha um papel fundamental na obtenção de resultados de usinagem precisos e eficientes.
A otimização dos parâmetros de corte, incluindo velocidades e avanços, profundidade de corte, fluidos de corte e gerenciamento da vida útil da ferramenta, é outro aspecto crítico do torneamento CNC. Ao selecionar cuidadosamente os parâmetros corretos, os maquinistas podem aumentar a produtividade, manter a longevidade da ferramenta e melhorar a qualidade do acabamento superficial.
Finalmente, ser capaz de solucionar problemas comuns de ajuste de ferramentas, como trepidação da ferramenta, acabamento superficial ruim, imprecisões dimensionais, problemas de controle de cavacos e quebra de ferramenta, é essencial para manter resultados de usinagem consistentes e de alta qualidade. A identificação desses problemas e a implementação de soluções adequadas garantem que o processo de usinagem permaneça tranquilo e eficiente.
No geral, uma compreensão abrangente das ferramentas de corte do torno e sua configuração, combinada com a capacidade de otimizar os parâmetros de corte e solucionar problemas, capacita os maquinistas a alcançar os melhores resultados nas operações de torneamento CNC. Aprendizado, treinamento e experiência contínuos são fundamentais para aprimorar essas habilidades e garantir processos de usinagem bem-sucedidos.
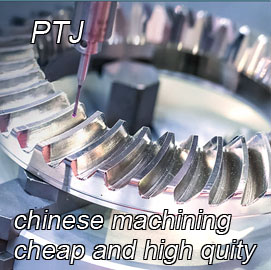
- 5 eixos de usinagem
- Fresagem CNC
- Torneamento CNC
- Indústrias de usinagem
- Processo de usinagem
- Tratamento da superfície
- Usinagem de Metal
- Usinagem de Plástico
- Molde de metalurgia do pó
- Fundição
- Galeria de peças
- Peças de metal automotivo
- Peças de máquinas
- Dissipador de calor LED
- Peças de Construção
- Peças Móveis
- Peças Médicas
- Partes eletrônicas
- Usinagem Sob Medida
- Peças de bicicleta
- Usinagem de Alumínio
- Usinagem de titânio
- Usinagem de aço inoxidável
- Usinagem de cobre
- Usinagem de latão
- Usinagem de Super Liga
- Peek Usinagem
- Usinagem UHMW
- Usinagem Unilate
- PA6 Usinagem
- Usinagem PPS
- Usinagem de Teflon
- Usinagem Inconel
- Usinagem de aço ferramenta
- Mais material