O desenvolvimento e a tendência da tecnologia de fusão por indução a vácuo
Com o rápido desenvolvimento da tecnologia industrial moderna, os requisitos das pessoas para o uso de peças mecânicas estão cada vez mais altos, e o ambiente de uso mais severo apresenta requisitos mais elevados para resistência a altas temperaturas, resistência ao desgaste, resistência à fadiga e outras propriedades dos materiais metálicos .
Para alguns metais específicos ou materiais de liga, seja um teste de P&D em estágio inicial ou produção em massa em estágio posterior e colocados em uso, pesquisa ou obtenção de materiais de liga metálica de alto desempenho requerem o suporte de equipamento de fundição de metal, equipamento de tratamento térmico de superfície, etc. Devido aos muitos métodos especiais de aquecimento ou fundição, a tecnologia de aquecimento por indução é usada para fundir e preparar materiais metálicos ou para sinterizar e tratar termicamente materiais em um determinado processo, que desempenhou um papel vital.
Este artigo apresenta o processo de desenvolvimento da tecnologia de fundição por indução a vácuo e a aplicação da tecnologia de fundição por indução em diferentes ocasiões. De acordo com a estrutura dos diferentes tipos de fornos de indução a vácuo, compare suas vantagens e desvantagens. Olhando para a direção de desenvolvimento futuro de fornos de indução a vácuo, expõe sua tendência de desenvolvimento. O desenvolvimento e o progresso dos fornos de indução a vácuo se refletem principalmente na melhoria gradual da estrutura geral do equipamento, na tendência cada vez mais óbvia de modularização e no sistema de controle mais inteligente.
1. Tecnologia de fusão por indução a vácuo
1.1 Princípio
__kindeditor_temp_url__A tecnologia de aquecimento por indução geralmente se refere a uma tecnologia que usa o princípio da indução eletromagnética para obter corrente de indução para materiais com melhor sensibilidade magnética para atingir o propósito de aquecimento sob condições de vácuo. A corrente elétrica passa através da bobina eletromagnética que envolve o material metálico em uma certa frequência. A mudança da corrente elétrica gera um campo magnético induzido, que causa uma corrente induzida no metal e gera uma grande quantidade de calor para aquecer o material. Quando o calor é relativamente baixo, ele pode ser usado no tratamento térmico por indução a vácuo e em outros processos. Quando o calor é alto, o calor gerado é suficiente para derreter o metal e ser usado para preparar materiais metálicos ou ligas.
1.2, aplicação
1.2.1, fusão por indução a vácuo
A tecnologia de fusão por indução a vácuo é atualmente a tecnologia de aquecimento por indução mais eficiente, rápida, de baixo consumo, com economia de energia e ambientalmente amigável para o aquecimento de materiais metálicos. Essa tecnologia é implementada principalmente em fornos de fusão por indução e outros equipamentos e tem uma ampla gama de aplicações. As matérias-primas de metal sólido são colocadas em um cadinho envolto por uma bobina. Quando a corrente flui através da bobina de indução, uma força eletromotriz induzida é gerada e uma corrente parasita é gerada dentro da carga de metal. Quando o calor atual é maior que a taxa de dissipação de calor da carga metálica, o calor se acumula mais e mais. Ao atingir um determinado nível, o metal derrete do estado sólido ao estado líquido para atingir o propósito de fundir metais. Neste processo, uma vez que todo o processo ocorre em um ambiente de vácuo, é benéfico remover as impurezas do gás de dentro do metal, e o material da liga metálica obtido é mais puro. Ao mesmo tempo, durante o processo de fundição, por meio do controle do ambiente de vácuo e do aquecimento por indução, a temperatura de fundição pode ser ajustada e a liga de metal pode ser complementada a tempo de atingir o objetivo de refino. Durante o processo de fusão, devido às características da tecnologia de fusão por indução, o material de metal líquido dentro do cadinho pode ser agitado automaticamente devido à interação da força eletromagnética para tornar a composição mais uniforme. Esta também é uma grande vantagem da tecnologia de fusão por indução.
Comparada com a fundição tradicional, a fundição por indução a vácuo tem grandes vantagens devido à economia de energia, proteção ambiental, bom ambiente de trabalho para os trabalhadores e baixa intensidade de trabalho. Usando a tecnologia de fusão por indução, o material da liga final é menos impureza e a proporção da liga adicionada é mais adequada, o que pode atender melhor aos requisitos do processo para as propriedades do material.
A tecnologia de fundição por indução a vácuo tem sido usada em grande escala, desde fornos de indução de vários quilos para pesquisa experimental até fornos de indução em grande escala com capacidade de dezenas de toneladas para produção real. Devido à sua tecnologia de operação simples, o processo de fusão é fácil de controlar e a temperatura de fusão é rápida. , O metal fundido tem as vantagens de composição uniforme e tem grandes perspectivas de aplicação, tendo se desenvolvido rapidamente nos últimos anos.
1.2.2, sinterização por indução a vácuo
A sinterização a vácuo refere-se à sinterização de metal, liga ou pó de composto metálico em produtos de metal e pedaços de metal a uma temperatura abaixo do ponto de fusão em um ambiente com um grau de vácuo de (10-10-3Pa). Sinterizando sob condições de vácuo, não há reação entre o metal e o gás, e nenhuma influência do gás adsorvido. Não apenas o efeito de densificação é bom, mas também pode desempenhar um papel de purificação e redução, reduzindo a temperatura de sinterização e a proporção de sinterização à temperatura ambiente pode ser reduzida em 100 ℃ ~ 150 ℃, Economize consumo de energia, melhore a vida útil do forno de sinterização e obtenção de produtos de alta qualidade.
Para alguns materiais, é necessário realizar a ligação entre as partículas através da transferência de átomos por aquecimento, e a tecnologia de sinterização por indução desempenha um papel de aquecimento neste processo. A vantagem da sinterização por indução a vácuo é que ajuda a reduzir as substâncias nocivas (vapor d'água, oxigênio, nitrogênio e outras impurezas) na atmosfera sob condições de vácuo e evita uma série de reações como descarbonetação, nitretação, cementação, redução e oxidação . Durante o processo, a quantidade de gás nos poros é reduzida e a reação química das moléculas do gás é reduzida. Ao mesmo tempo, o filme de óxido na superfície do material é removido antes que o material apareça na fase líquida, de modo que o material é mais densamente ligado quando o material é fundido e ligado, e sua resistência ao desgaste é melhorada. força. Além disso, a sinterização por indução a vácuo também tem um certo efeito na redução dos custos do produto.
Como o conteúdo de gás é relativamente baixo em um ambiente de vácuo, a convecção e a condução de calor podem ser ignoradas. O calor é principalmente transferido do componente de aquecimento para a superfície do material na forma de radiação. A seleção é baseada na temperatura de sinterização específica e nas propriedades físicas e químicas do material. Componentes de aquecimento apropriados também são muito importantes. Comparado com o aquecimento por resistência a vácuo, a sinterização por indução adota aquecimento de energia de frequência intermediária, o que evita o problema de isolamento de alta temperatura dos fornos a vácuo que usam aquecimento por resistência até certo ponto.
Atualmente, a tecnologia de sinterização por indução é usada principalmente nas áreas de aço e metalurgia. Além disso, em materiais cerâmicos especiais, a sinterização por indução melhora a ligação de partículas sólidas, ajuda os grãos de cristal a crescer, comprime os vazios e, a seguir, aumenta a densidade para formar corpos sinterizados policristalinos densos. A tecnologia de sinterização por indução também está sendo mais amplamente utilizada na pesquisa de novos materiais.
1.2.3, tratamento térmico por indução a vácuo
No momento, deve haver mais tecnologia de tratamento térmico por indução, principalmente concentrada na tecnologia de endurecimento por indução. Coloque a peça dentro do indutor (bobina), quando uma corrente alternada de uma certa frequência passa pelo indutor, um campo magnético alternado será gerado ao seu redor. A indução eletromagnética do campo magnético alternado produz uma corrente parasita fechada na peça de trabalho. Devido ao efeito de pele, ou seja, a distribuição da corrente induzida na seção transversal da peça de trabalho é muito desigual, a densidade de corrente na superfície da peça de trabalho é muito alta e diminui gradualmente para o interior.
A energia elétrica da corrente de alta densidade na superfície da peça é convertida em energia térmica, que aumenta a temperatura da superfície, ou seja, realiza o aquecimento da superfície. Quanto mais alta a frequência da corrente, maior será a diferença de densidade da corrente entre a superfície e o interior da peça de trabalho e mais fina será a camada de aquecimento. Depois que a temperatura da camada de aquecimento ultrapassar a temperatura do ponto crítico do aço, ele é rapidamente resfriado para obter o resfriamento da superfície. Pode-se saber a partir do princípio do aquecimento por indução que a profundidade de penetração da corrente pode ser alterada apropriadamente ajustando a frequência da corrente através da bobina de indução. A profundidade ajustável também é uma grande vantagem do tratamento térmico por indução. No entanto, a tecnologia de endurecimento por indução não é adequada para peças mecânicas complicadas devido à sua pouca adaptabilidade. Embora a camada superficial da peça temperada tenha uma maior tensão compressiva interna, a resistência à fratura por fadiga é maior. Mas só é adequado para a produção em linha de montagem de peças simples.
Atualmente, a aplicação da tecnologia de endurecimento por indução é usada principalmente na têmpera de superfície de manivelaeixose cameixos na indústria automotiva. Embora essas peças tenham uma estrutura simples, mas o ambiente de trabalho é hostil, elas têm um certo grau de resistência ao desgaste, resistência à flexão e resistência ao desempenho das peças. Requisitos de fadiga, através do endurecimento por indução para melhorar sua resistência ao desgaste e resistência à fadiga também é o método mais razoável para atender aos requisitos de desempenho. É amplamente utilizado no tratamento de superfície de algumas peças da indústria automotiva.
2. Equipamento de fusão por indução a vácuo
O equipamento de fundição por indução a vácuo usa tecnologia de fundição por indução para realizar o princípio em uso real por meio da combinação da estrutura mecânica. O equipamento geralmente usa o princípio de indução eletromagnética para colocar a bobina de indução e o material em uma cavidade fechada e extrair o gás do recipiente por meio de um sistema de bombeamento a vácuo e, em seguida, usar a fonte de alimentação para passar a corrente através da bobina de indução para gerar uma força eletromotriz induzida e estar dentro do material Um vórtice é formado, e quando a geração de calor atinge um determinado nível, o material começa a derreter. Durante o processo de fusão, uma série de operações, como controle de potência, medição de temperatura, medição de vácuo e alimentação suplementar são realizadas por meio de outros componentes de suporte no equipamento e, finalmente, o metal líquido é derramado no molde através da inversão do cadinho para formar um lingote de metal. Smelt. A estrutura principal do equipamento de fusão por indução a vácuo inclui as seguintes partes:
Além dos componentes acima, o forno de fusão a vácuo também deve ser equipado com uma fonte de alimentação, um sistema de controle e um sistema de resfriamento para fornecer energia para o equipamento derreter o material e fornecer uma certa quantidade de resfriamento nas peças-chave para evitar que o sistema superaqueça e resulte em redução de vida ou danos estruturais. Para equipamentos de fundição por indução com requisitos de processo específicos, existem componentes auxiliares relacionados, como carrinho de transmissão, abertura e fechamento da porta do forno, bandeja de fundição centrífuga, janela de observação, etc. Para equipamentos com mais impurezas, também deve ser equipado com um filtro de gás sistema, etc. Pode ser visto que, além dos componentes necessários, um conjunto completo de equipamento de fusão por indução também pode realizar diferentes funções ao adicionar outros componentes de acordo com requisitos de processo específicos e fornecer condições convenientes e métodos de implementação para preparação de metal.
2.1. Forno de fusão por indução a vácuo
O forno de fundição por indução a vácuo é um equipamento de fundição que primeiro derrete o metal por aquecimento por indução sob vácuo e, em seguida, derrama o metal líquido em um molde para obter um lingote de metal. O desenvolvimento de fornos de indução a vácuo começou por volta de 1920 e era usado principalmente para fundir ligas de níquel-cromo. Até a Segunda Guerra Mundial promover o avanço da tecnologia de vácuo, o forno de fusão por indução a vácuo estava realmente desenvolvido. Durante este período, devido à demanda por materiais de liga, os fornos de fusão por indução a vácuo continuaram a se desenvolver em grande escala, das várias toneladas iniciais a dezenas de toneladas de fornos de indução ultra-grandes. Para se adaptar à produção em massa, além da mudança na capacidade do equipamento, a estrutura do forno de indução também evoluiu de um forno de ciclo com um ciclo como uma unidade para uma fusão por indução a vácuo contínua ou semicontínua para carregamento, molde operações de preparação, fundição e vazamento. A operação contínua sem parar o forno economiza o tempo de carregamento e o tempo de espera do lingote para esfriar. A produção contínua aumenta a eficiência e também aumenta a produção de liga. Atenda melhor às necessidades de produção real. Em comparação com países estrangeiros, os primeiros fornos de indução a vácuo em meu país têm capacidade relativamente pequena, principalmente abaixo de 2 toneladas. Os fornos de fundição em grande escala ainda dependem de importações do exterior. Com o desenvolvimento das últimas décadas, meu país também pode desenvolver sozinho fundição por indução a vácuo em larga escala. Fornalha, a fusão máxima chega a mais de dez toneladas. O forno de fusão por indução a vácuo VIM desenvolvido anteriormente, com estrutura simples, uso conveniente e baixo custo de manutenção, tem sido amplamente utilizado na produção real.
A forma básica de um forno de fusão por indução a vácuo. Os materiais metálicos são adicionados ao cadinho de fusão por meio de uma torre giratória. O outro lado é alinhado com o cadinho e a medição da temperatura é realizada inserindo o termopar no metal fundido. O metal fundido é acionado pelo mecanismo de rotação e derramado no molde de formação para realizar a fusão do metal. Todo o processo é simples e conveniente de operar. Cada fundição requer um ou dois trabalhadores para ser concluída. Durante o processo de fundição, o monitoramento da temperatura em tempo real e o ajuste da composição do material podem ser obtidos, e o material metálico final está mais de acordo com os requisitos do processo.
2.2. Forno a gás de membrana de indução a vácuo
Para certos materiais, não é necessário completar o vazamento em uma câmara de vácuo no processo, apenas a preservação do calor e a desgaseificação em um ambiente de vácuo são necessários. Com base no forno VIM, o forno a gás de membrana de indução a vácuo do forno de desgaseificação VID é desenvolvido gradualmente.
A principal característica do forno de desgaseificação por indução a vácuo é a estrutura compacta e o pequeno volume do forno. Um volume menor é mais propício para uma extração rápida de gás e um melhor vácuo. Comparado com fornos de desgaseificação convencionais, o equipamento tem volume relativamente pequeno, baixa perda de temperatura, melhor flexibilidade e economia e é adequado para alimentação de líquidos ou sólidos. O forno VID pode ser usado para a fundição e desgaseificação de aço especial e metais não ferrosos, e precisa ser derramado no molde sob as condições de um ambiente atmosférico ou uma atmosfera protetora. Todo o processo de fundição pode realizar a remoção de impurezas, como descarburação e refino de materiais, desidrogenação, desoxidação e dessulfuração, o que conduz ao ajuste preciso da composição química para atender aos requisitos do processo.
Sob uma certa condição de vácuo ou atmosfera protetora, o material metálico é gradualmente derretido pelo aquecimento do forno de desgaseificação por indução, e o gás interno pode ser removido neste processo. Se um gás de reação apropriado for adicionado ao processo, ele se combinará com o elemento carbono dentro do metal para gerar carbonetos gasosos a serem removidos do forno, atingindo o objetivo de descarbonetação e refino. No processo de vazamento, uma certa atmosfera protetora precisa ser introduzida para garantir que o material de metal que foi desgaseificado seja isolado do gás na atmosfera e, finalmente, a desgaseificação e o refino do material de metal sejam concluídos.
2.3. Forno de vazamento de desgaseificação por indução a vácuo
O forno de vazamento e desgaseificação por indução a vácuo é desenvolvido com base nas duas primeiras tecnologias de fundição. Em 1988, Leybold-Heraeus, o predecessor da empresa alemã ALD, fabricou o primeiro forno VIDP. O núcleo técnico deste tipo de forno é uma câmara compacta de fusão a vácuo integrada ao cadinho da bobina de indução. É apenas um pouco maior do que a bobina de indução e contém apenas a bobina de indução e o cadinho. Cabos, tubulações de resfriamento de água e mecanismo de rotação hidráulica são todos instalados fora da câmara de derretimento. A vantagem é proteger cabos e tubulações resfriadas a água de danos causados por respingos de aço fundido e mudanças periódicas de temperatura e pressão. Devido à conveniência de desmontagem e facilitar a substituição do cadinho, o corpo do forno VIDP é equipado com três corpos de forno. O revestimento do forno do cadinho de preparação encurta o ciclo de produção e melhora a eficiência da produção.
A tampa do forno é apoiada na estrutura do forno e duas colunas do cilindro hidráulico por vedação a vácuo rolamentos. Ao despejar, dois cilindros hidráulicos cobrem a tampa do forno na lateral, e a tampa do forno direciona a câmara de fusão para inclinar em torno do vácuo rolamento. No estado de vazamento inclinado, não há movimento relativo entre a câmara de fusão e o cadinho da bobina de indução. O corredor é uma parte importante do forno VIDP. Como o projeto do forno VIDP isola a câmara de fusão da câmara de lingote, o aço fundido deve passar pelo canal de vácuo para a câmara de lingote. A câmara do lingote é aberta e fechada com um lado quadrado oblíquo. É composto por duas partes. A parte fixa é adjacente à câmara de rotor e a parte móvel se move horizontalmente ao longo da trilha no solo para completar a abertura e o fechamento da câmara de lingote. Em alguns equipamentos, a parte móvel é projetada para ter 30 graus, aberta à esquerda e à direita para cima, o que é conveniente para carregar e descarregar lingoteiras e manutenção diária e reparo de guindastes. No início da fundição, o corpo do forno é levantado pelo mecanismo hidráulico abaixo, unido à tampa da estrutura superior do forno e travado com um mecanismo especial. A extremidade superior da tampa do forno é conectada com a câmara de alimentação por meio de um vácuo válvula.
Uma vez que apenas a parte de fundição é encerrada na câmara de vácuo e derramada através da ranhura de desvio, a estrutura do forno é compacta, a câmara de fundição é menor e o vácuo pode ser controlado melhor e mais rápido. Comparado com o forno de fusão por indução tradicional, possui as características de curto tempo de evacuação e baixa taxa de vazamento. O controle de pressão ideal pode ser alcançado equipando o sistema de controle lógico PLC. Ao mesmo tempo, o sistema de agitação eletromagnética pode agitar de forma estável a poça fundida e os elementos adicionados serão dissolvidos uniformemente na poça fundida de cima para baixo, mantendo a temperatura próxima da constante. Ao despejar dinheiro, o canal é aquecido pelo sistema de aquecimento externo para reduzir o bloqueio inicial de vazamento da porta de vazamento e a rachadura térmica do canal. Ao adicionar defletor de filtro e outras medidas, ele pode aliviar o impacto do aço fundido e melhorar a pureza do metal. Devido ao pequeno volume do forno VIDP, a detecção e o reparo de vazamento a vácuo são mais fáceis e o tempo de limpeza no forno é mais curto. Além disso, a temperatura no forno pode ser medida com um termopar pequeno e fácil de substituir.
2.4, cadinho de indução resfriado a água
O método de fundição por levitação a vácuo por indução eletromagnética de cadinho resfriado a água é um método de fundição que se desenvolveu rapidamente nos últimos anos. É usado principalmente para preparar materiais metálicos ou não metálicos de alto ponto de fusão, alta pureza e extremamente ativos. Ao cortar o cadinho de cobre em partes iguais da estrutura da pétala de cobre, e o resfriamento da água é passado através de cada bloco de pétala, esta estrutura aumenta o impulso eletromagnético, de modo que o metal fundido é espremido no meio para formar uma protuberância e se separar do parede do cadinho. O metal é colocado em um campo eletromagnético alternado. O dispositivo concentra a capacidade no espaço de volume dentro do cadinho e, em seguida, forma uma forte corrente parasita na superfície da carga. Por um lado, ele libera calor de Joule para derreter a carga e, por outro lado, forma a força de Lorentz para derreter. O corpo suspende e produz uma forte agitação. Os elementos de liga adicionados podem ser rápida e uniformemente misturados no fundido, tornando a composição química mais uniforme e a condução de temperatura mais equilibrada. Devido ao efeito de levitação magnética, o fundido fica fora de contato com a parede interna do cadinho, o que evita que o cadinho polua o fundido. Ao mesmo tempo, reduz a condução de calor e aumenta a radiação de calor, o que reduz a dissipação de calor do metal fundido e atinge uma temperatura mais alta. Para a carga de metal adicionada, ele pode ser derretido e mantido aquecido de acordo com o tempo necessário e a temperatura definida, e a carga não precisa ser processada com antecedência. A fundição de cadinhos resfriados a água pode atingir o nível de fundição por feixe de elétrons em termos de remoção de inclusões de metal e refino de desgaseificação, enquanto a perda por evaporação é menor e o consumo de energia é menor e a eficiência de produção é melhorada. Devido às características de aquecimento sem contato do aquecimento por indução, o impacto no fundido é menor e tem um bom efeito na preparação de metais de maior pureza ou extremamente ativos. Devido à estrutura complexa do equipamento, ainda é difícil realizar a fundição maglev para equipamentos de grande capacidade. Neste estágio, não há nenhum equipamento de fundição de cadinho de cobre resfriado a água de grande capacidade. O atual equipamento de cadinho resfriado a água é usado apenas para pesquisa experimental em fundição de metal de pequeno volume.
3. A tendência de desenvolvimento futuro de equipamentos de fusão por indução
Com o desenvolvimento da tecnologia de aquecimento por indução a vácuo, os tipos de fornos estão mudando constantemente para atingir diferentes funções. De uma simples estrutura de fundição ou aquecimento, gradualmente se desenvolveu em uma estrutura complexa que pode realizar diferentes funções e é mais propícia à produção. Para processos tecnológicos mais complexos no futuro, como alcançar um controle de processo preciso, medir e extrair informações relevantes e reduzir os custos de mão de obra tanto quanto possível é a direção de desenvolvimento do equipamento de fusão por indução.
3.1, modular
Em um conjunto completo de equipamentos, diferentes componentes são equipados para diferentes requisitos de uso. Cada parte do componente executa sua própria função para atingir seu próprio propósito de uso. Para certos tipos de fornos, adicionar certos módulos para tornar o equipamento mais completo, por exemplo, equipado com um sistema completo de medição de temperatura ajuda a observar as mudanças dos materiais no forno com a temperatura, e conseguir um controle mais razoável da temperatura; equipado com espectrômetro de massa para detectar a composição do material Ajuste o tempo e a sequência de adição dos elementos de liga para melhorar o desempenho da liga na fase de desenvolvimento do processo; equipado com um canhão de elétrons e canhão de íons para resolver o problema de derretimento de alguns metais refratários, e assim por diante. No futuro equipamento metalúrgico de indução, diferentes combinações de diferentes módulos para atingir diferentes funções e atender diferentes requisitos de processo tornaram-se uma tendência inevitável de desenvolvimento, e também é uma combinação e referência de diferentes campos. Com o objetivo de aprimorar o processo de fundição de metais e obter materiais com melhor desempenho, os equipamentos modulares terão maior competitividade no mercado.
3.2. Controle inteligente
Comparado com a fundição tradicional, o equipamento de indução a vácuo tem uma grande vantagem em realizar o controle do processo. Devido ao desenvolvimento da tecnologia de computador, a operação amigável da interface homem-máquina, aquisição de sinal inteligente e configuração de programa razoável no equipamento podem facilmente atingir o objetivo de controlar o processo de fundição, reduzir custos de mão de obra e tornar a operação mais simples e conveniente.
No desenvolvimento futuro, sistemas de controle mais inteligentes serão adicionados ao equipamento de vácuo. Para o processo estabelecido, será mais fácil para as pessoas controlar com precisão a temperatura de fundição por meio do sistema de controle inteligente, adicionar materiais de liga em um momento específico e concluir uma série de ações de fundição, preservação de calor e vazamento. E tudo isso será controlado e registrado pelo computador, reduzindo perdas desnecessárias causadas por erros humanos. Para o processo de fundição repetitivo, pode realizar um controle moderno mais conveniente e inteligente.
3.3. Informatização
O equipamento de fundição por indução irá gerar uma grande quantidade de informações de fundição durante todo o processo de fundição, as mudanças de parâmetro em tempo real da fonte de alimentação de aquecimento por indução, o campo de temperatura da carga, o cadinho, o campo eletromagnético gerado pela bobina de indução, o propriedades físicas do metal fundido e assim por diante. Atualmente, o equipamento realiza apenas uma coleta de dados simples, e o processo de análise é realizado após a extração dos dados após a conclusão da fundição. No futuro, o desenvolvimento da informatização, coleta e processamento de dados e o processo de análise estarão inevitavelmente quase sincronizados com o processo de fundição. Coleta de dados completa para os materiais fundidos internamente de equipamentos metalúrgicos, processamento de dados por computador, exibição em tempo real do campo de temperatura interna e campo eletromagnético do equipamento na situação atual e transmissão de sinal, por meio de feedback em tempo real de diferentes dados, conveniente para as pessoas A observação em tempo real e o ajuste do processo de fundição reforçaram a intervenção e o controle humanos. No processo de fundição, ajustes oportunos são feitos para melhorar o processo e melhorar o desempenho da liga.
Conclusão 4
Com o progresso da indústria, a tecnologia de fusão por indução a vácuo se desenvolveu tremendamente nas últimas décadas com suas vantagens exclusivas e desempenha um papel importante no campo industrial. No momento, embora a tecnologia de fundição por indução a vácuo do meu país ainda esteja atrasada em relação aos países estrangeiros, ainda requer os esforços incessantes de profissionais relevantes para melhorar a competitividade do mercado de equipamentos de fundição especiais do meu país e tentar o seu melhor para se tornar o equipamento de fundição de primeira classe do mundo . Forefront.
Link para este artigo: O desenvolvimento e a tendência da tecnologia de fusão por indução a vácuo
Declaração de reimpressão: Se não houver instruções especiais, todos os artigos neste site são originais. Indique a fonte para reimpressão: https: //www.cncmachiningptj.com
PTJ® é um fabricante personalizado que oferece uma gama completa de barras de cobre, partes de latão e partes de cobre. Os processos de fabricação comuns incluem cunhagem, gravação em relevo, coppersmithing, serviços de edm com fio, gravura, formação e dobra, perturbação, quente forjamento e prensagem, perfuração e puncionamento, enrolamento e recartilhamento de linha, cisalhamento, usinagem multi-fuso, extrusão e forjamento de metal e estampagem. As aplicações incluem barramentos, condutores elétricos, cabos coaxiais, guias de ondas, componentes de transistores, tubos de microondas, tubos de molde vazio e metalurgia do pó tanques de extrusão.
Conte-nos um pouco sobre o orçamento do seu projeto e prazo de entrega previsto. Vamos traçar estratégias com você para fornecer os serviços mais econômicos para ajudá-lo a atingir seu objetivo. Você está convidado a nos contatar diretamente ( vendas@pintejin.com ).
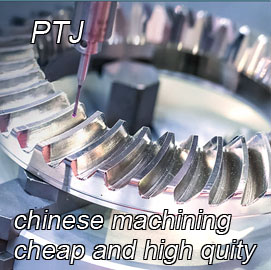
- 5 eixos de usinagem
- Fresagem CNC
- Torneamento CNC
- Indústrias de usinagem
- Processo de usinagem
- Tratamento da superfície
- Usinagem de Metal
- Usinagem de Plástico
- Molde de metalurgia do pó
- Fundição
- Galeria de peças
- Peças de metal automotivo
- Peças de máquinas
- Dissipador de calor LED
- Peças de Construção
- Peças Móveis
- Peças Médicas
- Partes eletrônicas
- Usinagem Sob Medida
- Peças de bicicleta
- Usinagem de Alumínio
- Usinagem de titânio
- Usinagem de aço inoxidável
- Usinagem de cobre
- Usinagem de latão
- Usinagem de Super Liga
- Peek Usinagem
- Usinagem UHMW
- Usinagem Unilate
- PA6 Usinagem
- Usinagem PPS
- Usinagem de Teflon
- Usinagem Inconel
- Usinagem de aço ferramenta
- Mais material